2025 Autor: Howard Calhoun | [email protected]. Última modificação: 2025-01-24 13:23
Um forno a arco de aço (EAF) é um dispositivo que aquece o material por flexão elétrica.
Os aparelhos industriais variam em tamanho, desde pequenas unidades, cerca de uma tonelada de energia (usada em fundições para fazer produtos de ferro fundido) até 400 unidades por tonelada, usadas para reciclagem de aço. Os fornos de aço a arco, EAF, usados em laboratórios de pesquisa podem ter capacidade de apenas algumas dezenas de gramas. A temperatura dos dispositivos industriais pode chegar a 1800 °C (3272 °F), enquanto as instalações laboratoriais excedem 3000 °C (5432 °F).
Fornos de aço a arco (EAFs) diferem dos fornos de indução, pois o material que está sendo carregado é submetido diretamente à flexão elétrica e a corrente nos terminais passa pelo material carregado.
Construção
Forno de aço a arco é utilizado para produção de aço e é composto por um vaso refratário. Principalmente dividido em três seções:
- Shell, que consiste em paredes laterais e aço inferiortigelas.
- Palete que é feito de material refratário.
- Telhado. Pode ser com forro resistente ao calor ou refrigerado a água. E também é feito na forma de uma bola ou de um cone truncado (seção cônica). A cobertura também suporta um delta refratário em seu centro por onde entram um ou mais eletrodos de grafite.
Itens individuais
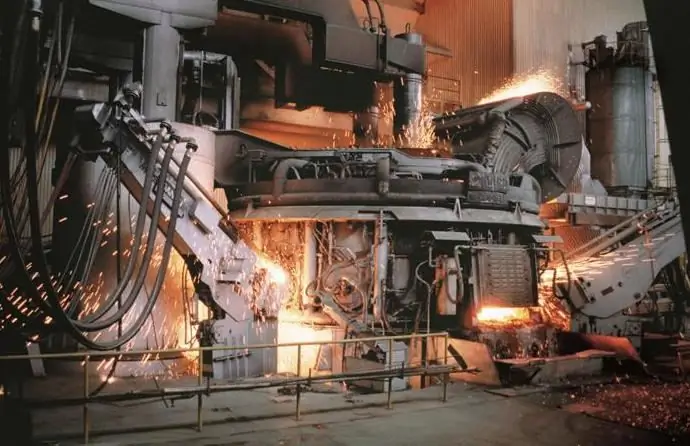
A fornalha pode ter formato hemisférico e é necessária em um forno excêntrico para rosquear o fundo. Nas oficinas modernas, o forno de aço a arco - EAF 5 - é frequentemente elevado acima do piso térreo para que as conchas e os potes de escória possam ser facilmente manobrados em ambas as extremidades. Separado da estrutura está o suporte do eletrodo e o sistema elétrico, bem como a plataforma inclinada sobre a qual o instrumento fica.
Ferramenta única
Um forno a arco típico de fundição de aço EAF 3 é alimentado por uma fonte trifásica e, portanto, possui três eletrodos. Possuem seção redonda e, via de regra, segmentos com conexões rosqueadas, para que, à medida que se desgastam, novos elementos possam ser adicionados.
O arco é formado entre o material carregado e o eletrodo. A carga é aquecida tanto pela corrente que passa por ela quanto pela energia irradiada liberada pela onda. A temperatura atinge cerca de 3.000 °C (5.000 °F), fazendo com que as seções inferiores dos eletrodos brilhem como lâmpadas incandescentes quando o forno a arco está operando.
Os elementos são levantados e abaixados automaticamente por um sistema de posicionamento que pode usar qualquerguincho, guinchos ou cilindros hidráulicos. A regulação mantém uma corrente aproximadamente constante. Qual é o consumo de energia de um forno a arco? Ele é mantido constante durante a fusão da carga, mesmo que a sucata possa se mover sob os eletrodos à medida que derrete. As mangas do mastro que seguram o elemento podem carregar barramentos pesados (que podem ser tubos de cobre ocos resfriados a água fornecendo corrente para os grampos) ou "mangas quentes" onde todo o topo carrega a carga, aumentando a eficiência.
Este último tipo pode ser feito de aço cobreado ou alumínio. Grandes cabos refrigerados a água conectam barramentos ou suportes a um transformador localizado próximo ao forno. Uma ferramenta semelhante é instalada no armazenamento e resfriada com água.
Toque e outras operações
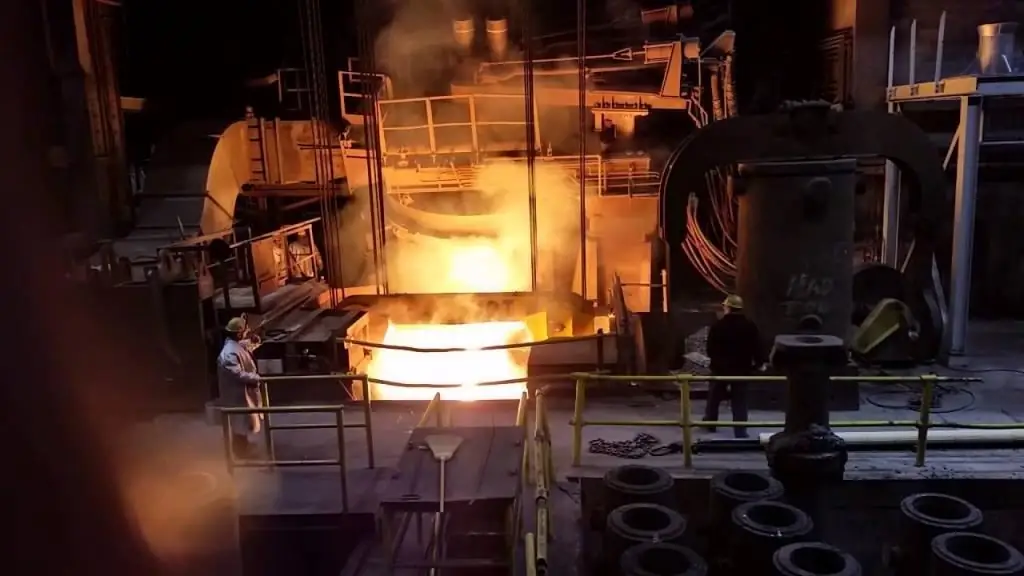
O forno a arco de aço EAF 50 é construído em uma plataforma inclinada para que o aço líquido possa ser despejado em outro recipiente para transporte. A operação de inclinação para transferir o aço fundido é chamada de rosqueamento. Inicialmente, todas as abóbadas siderúrgicas do forno a arco tinham uma calha de descarga coberta com refratário, que era lavada quando era inclinada.
Mas muitas vezes os equipamentos modernos possuem uma válvula de saída inferior excêntrica (EBT) para reduzir a incorporação de nitrogênio e escória no aço líquido. Estes fornos têm uma abertura que atravessa verticalmente a lareira e a casca e está descentralizada numa "bica" estreita em forma de ovo. está cheioareia refratária.
As plantas modernas podem ter duas conchas com um conjunto de eletrodos que são passados entre elas. A primeira parte aquece a sucata, enquanto a outra é usada para derreter. Outros fornos CC têm um layout semelhante, mas possuem eletrodos para cada bainha e um conjunto de componentes eletrônicos.
Elementos de oxigênio
Os fornos AC geralmente têm um padrão de pontos quentes e frios ao longo do perímetro da fornalha, localizados entre os eletrodos. Nos modernos, os queimadores de oxi-combustível são instalados na parede lateral. Eles são usados para fornecer energia química para zonas negativas, o que torna o aquecimento do aço mais uniforme. A energia adicional é fornecida pelo fornecimento de oxigênio e carbono ao forno. Historicamente, isso era feito com lanças (tubos ocos de aço macio) na porta de escória, agora é feito principalmente com unidades de injeção montadas na parede que combinam queimadores de oxi-combustível e sistemas de suprimento de ar em um recipiente.
Um moderno forno de aço de médio porte possui um transformador de cerca de 60.000.000 volt-amps (60 MVA), com uma tensão secundária de 400 a 900 e uma corrente superior a 44.000. espera-se que o forno produza 80 toneladas métricas de aço líquido em cerca de 50 minutos, desde o carregamento de sucata fria até a extração.
Em comparação, os fornos básicos de oxigênio podem ter uma capacidade de 150-300 toneladas por lote ou "aquecer" e gerar calor por 30-40 minutos. Existem enormes diferenças nos detalhes do projeto e operação do forno,dependendo do produto final e das condições locais, bem como pesquisas contínuas para melhorar a eficiência da planta.
A maior sucata (em termos de peso de derivação e classificação do transformador) é um dispositivo DC exportado do Japão com um peso de derivação de 420 toneladas métricas e alimentado por oito transformadores de 32 MVA para uma potência total de 256 MBA.
É preciso aproximadamente 400 quilowatts-hora para produzir uma tonelada de aço em um forno elétrico a arco, ou cerca de 440 kWh por métrica. A energia mínima teórica necessária para fundir sucata de aço é de 300 kWh (ponto de fusão 1520 °C / 2768 °F). Portanto, um EAF de 300 toneladas com potência de 300 MVA exigirá cerca de 132 MWh de energia e o tempo de ativação é de aproximadamente 37 minutos.
A produção de aço por arco elétrico só é economicamente viável se houver eletricidade suficiente com uma rede bem desenvolvida. Em muitos lugares, as usinas operam fora do horário de pico, quando as concessionárias têm excesso de capacidade de produção e o preço por metro é menor.
Operação
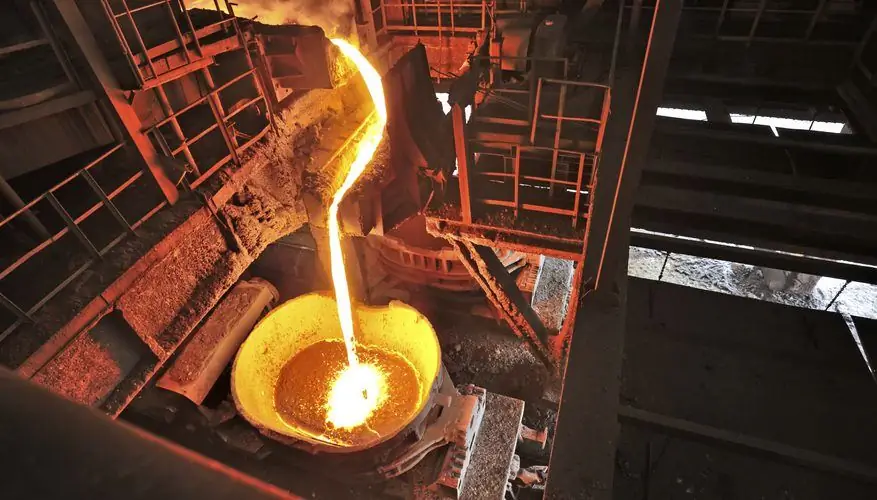
O forno de aço a arco despeja aço em uma pequena máquina de concha. A sucata de metal é entregue em um recesso localizado próximo à fundição. A sucata tende a se apresentar em duas variedades principais: sucata (produtos da linha branca, carros e outros itens feitos deaço leve) e fundido pesado (grandes lajes e vigas), bem como algum ferro reduzido direto (DRI) ou ferro gusa para equilíbrio químico. Fornos separados derretem quase 100% DRI.
Próximo passo
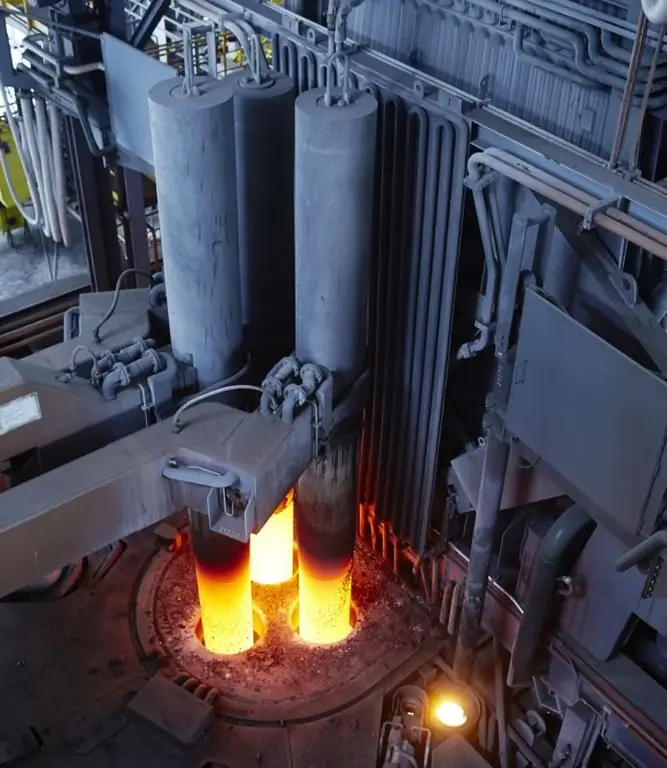
A sucata é carregada em grandes baldes, chamados cestos, com portas tipo garra para a base. Cuidados devem ser tomados para garantir que a sucata esteja na cesta para garantir o bom funcionamento do forno. Um forte derretimento é colocado no topo com uma leve camada de um fragmento protetor, sobre o qual outra parte fica. Todos eles devem estar presentes no forno após o carregamento. Nesse momento, a cesta pode ser movida para o pré-aquecedor de sucata, que usa os gases quentes da fundição para recuperar energia, melhorando a eficiência.
Estouro
Em seguida, o navio é levado para a fundição, o teto do forno é aberto e o material é carregado nele. A transferência é uma das operações mais perigosas para os operadores. Muita energia potencial é liberada por toneladas de metal caindo. Qualquer matéria líquida no forno é frequentemente empurrada para cima e para fora por sucata sólida e graxa. A poeira no metal inflama se o forno estiver quente, causando a erupção de uma bola de fogo.
Em alguns dispositivos de dupla camada, a sucata é carregada no segundo enquanto o primeiro está derretendo e é pré-aquecido pelo gás de exaustão da parte ativa. Outras operações são: carregamento contínuo e trabalho com temperatura em uma esteira transportadora, que então descarrega o metal no próprio forno. Outros dispositivos podem inicializarsubstância quente de outras operações.
Tensão
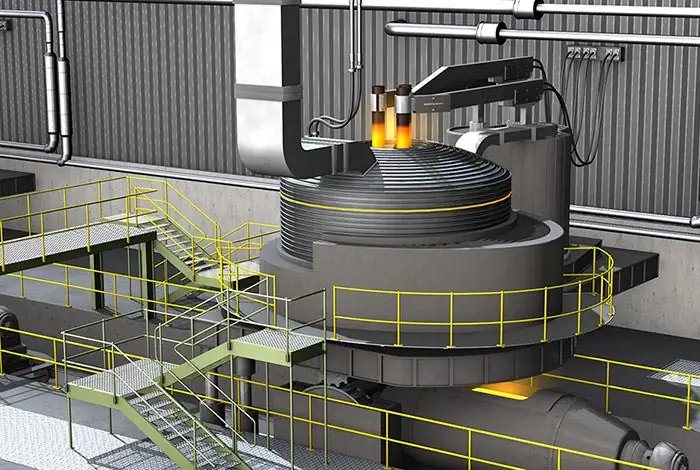
Após o carregamento, o teto se inclina sobre a fornalha e o derretimento começa. Os eletrodos são abaixados sobre a sucata, um arco é criado e, em seguida, são colocados de modo que se espalhem na camada de migalhas na parte superior do dispositivo. Baixas tensões são selecionadas para esta operação para proteger o telhado e as paredes do calor excessivo e danos causados pelo arco.
Uma vez que os eletrodos atingiram o fundido pesado na base do forno e as ondas são blindadas pelo pé de cabra, a tensão pode ser aumentada e os eletrodos levantados ligeiramente, alongando e aumentando a potência do fundido. Isso permite que a poça derretida se forme mais rapidamente, reduzindo o tempo de retirada.
Oxigênio é soprado em sucata, queimando ou cortando aço, e calor químico adicional é fornecido por queimadores de parede. Ambos os processos aceleram a fusão da substância. Bicos supersônicos permitem que jatos de oxigênio penetrem na escória espumante e alcancem o banho líquido.
Oxidação de impurezas
Uma parte importante da siderurgia é a formação de escória que flutua na superfície do aço fundido. Geralmente é composto por óxidos metálicos e também atua como local de coleta de impurezas oxidadas, como manta térmica (impedindo a perda excessiva de calor) e também ajuda a reduzir a erosão do revestimento refratário.
Para um forno com refratários básicos produzindo aço carbono, os formadores de escória comuns são o óxido de cálcio (CaO na forma de calcinadocal) e magnésio (MgO na forma de dolomita e magnesita). Essas substâncias são carregadas com sucata ou sopradas no forno durante a fusão.
Outro componente importante é o óxido de ferro, formado quando o aço é queimado com a introdução de oxigênio. Mais tarde, quando aquecido, o carbono (na forma de carvão) é injetado nessa camada, reagindo com o óxido de ferro para formar metal e monóxido de carbono. Isso resulta na formação de espuma da escória, resultando em maior eficiência térmica. O revestimento evita danos no teto e nas paredes laterais do forno devido ao calor radiante.
Combustão de impurezas
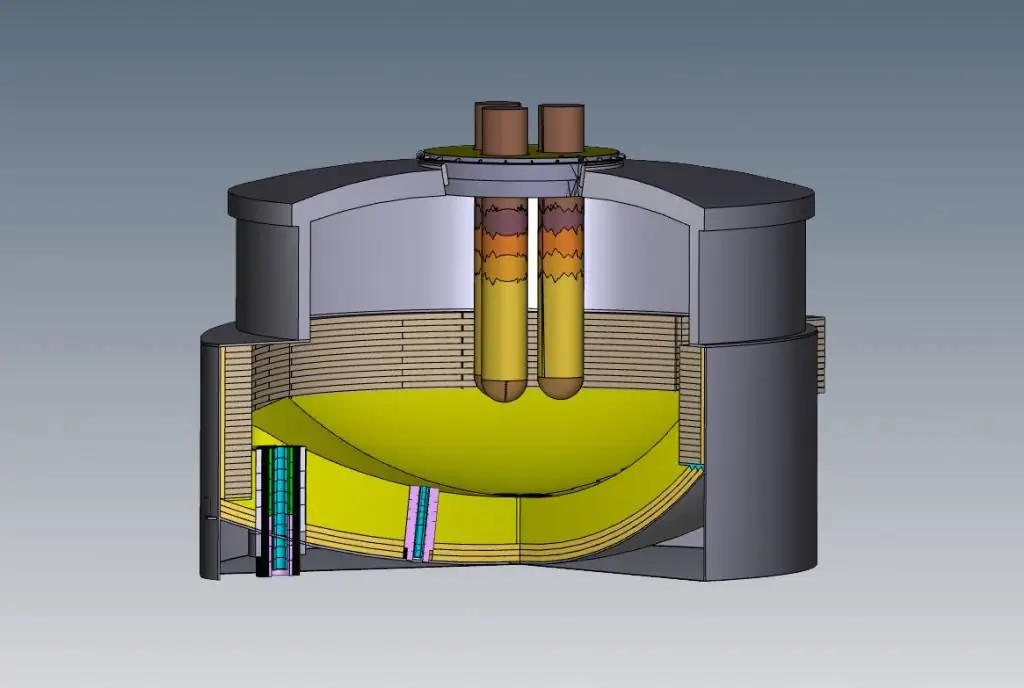
Uma vez que a sucata é completamente derretida e uma poça plana é alcançada, outro balde pode ser carregado no forno. Após a segunda carga estar completamente fundida, são realizadas operações de refino para verificar e corrigir a composição química do aço e superaquecer o fundido acima de seu ponto de congelamento em preparação para o rosqueamento. Mais formadores de escória são introduzidos e muito oxigênio entra no banho, queimando impurezas como silício, enxofre, fósforo, alumínio, manganês e cálcio, e removendo seus óxidos em escória.
A remoção do carbono ocorre depois que esses elementos queimam primeiro, pois são mais semelhantes ao oxigênio. Metais que possuem afinidade menor que o ferro, como níquel e cobre, não podem ser removidos por oxidação e só devem ser controlados por meio de química. Trata-se, por exemplo, da introdução do ferro reduzido direto e do ferro fundido mencionado anteriormente.
Escória espumosapersiste por toda parte e muitas vezes transborda o forno para transbordar da porta para o poço pretendido. A medição da temperatura e a seleção química são realizadas usando lanças automáticas. Oxigênio e carbono podem ser medidos mecanicamente com sondas especiais que são imersas em aço.
Benefícios de Produção
Usando um sistema de controle para fornos a arco de fundição de aço, é possível produzir aço a partir de 100% de matéria-prima - sucata. Isso reduz bastante a energia necessária para produzir a substância, em comparação com a produção primária de minérios.
Outro benefício é a flexibilidade: enquanto os altos-fornos não podem variar significativamente e podem funcionar por anos, este pode ser iniciado e desligado rapidamente. Isso permite que a siderúrgica varie a produção com base na demanda.
Forno de aço a arco típico é a fonte de aço para mini-mill, que pode produzir produtos em barra ou tiras. As mini-fundições podem estar localizadas relativamente perto dos mercados de aço e os requisitos de transporte são menores do que para uma planta integrada, que geralmente está localizada perto da costa para acesso ao transporte.
Dispositivo de Forno de Aço Arco
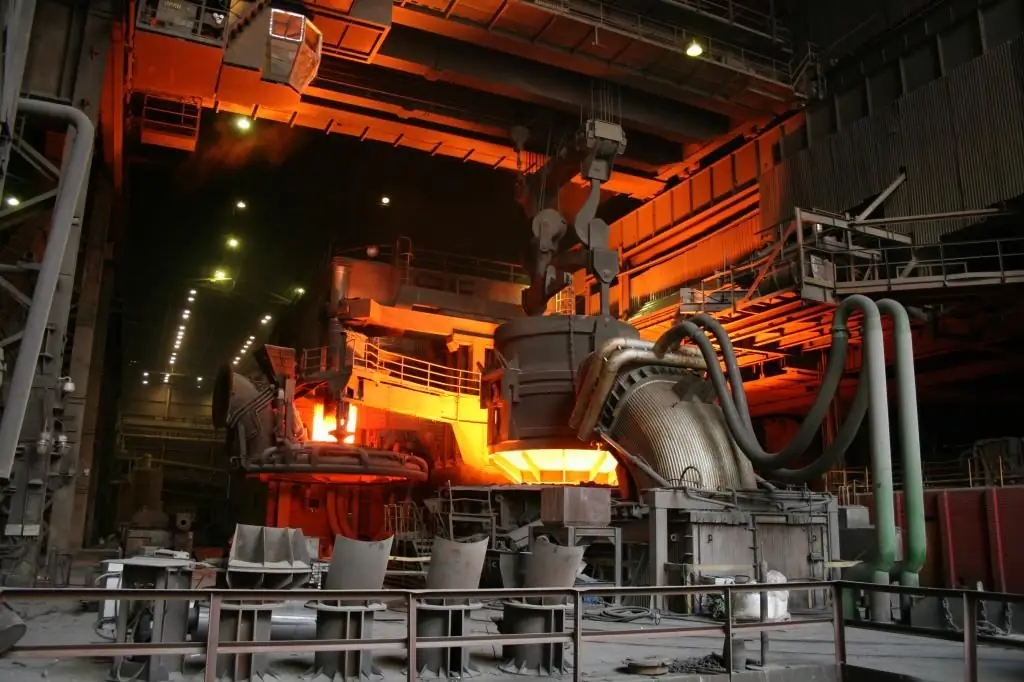
A seção transversal esquemática é um eletrodo que é levantado e abaixado por um acionamento de pinhão e cremalheira. A superfície é revestida com tijolos refratários e revestimento de fundo. A porta permite o acesso ao interiorpartes do dispositivo. O corpo do forno repousa sobre os balancins para que possa ser inclinado para bater.
Recomendado:
Aço inoxidável alimentar: GOST. Como identificar o aço inoxidável de qualidade alimentar? Qual é a diferença entre o aço inoxidável alimentar e o aço inoxidável técnico?

O artigo fala sobre tipos de aço inoxidável de qualidade alimentar. Leia como distinguir o aço inoxidável alimentar do técnico
Aço resistente à corrosão. Graus de aço: GOST. Aço inoxidável - preço
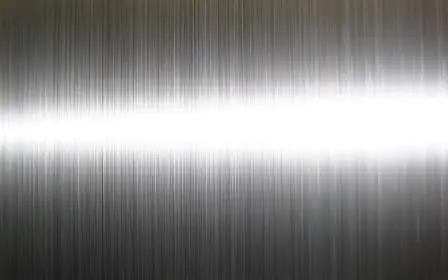
Por que os materiais metálicos se quebram. O que são aços e ligas resistentes à corrosão. Composição química e classificação de acordo com o tipo de microestrutura do aço inoxidável. Fatores que afetam o preço. Sistema de designação de grau de aço (requisitos GOST). Area de aplicação
O que é potência reativa? Compensação de potência reativa. Cálculo de potência reativa
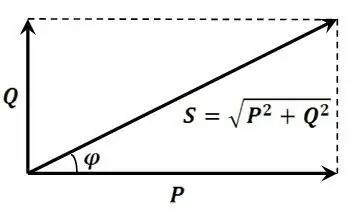
Em condições reais de produção, prevalece a potência reativa de natureza indutiva. As empresas instalam não um medidor elétrico, mas dois, um dos quais está ativo. E pelo gasto excessivo de energia “perseguida” em vão pelas linhas de energia, as autoridades competentes são multadas impiedosamente
Laser de fibra de itérbio: dispositivo, princípio de funcionamento, potência, produção, aplicação
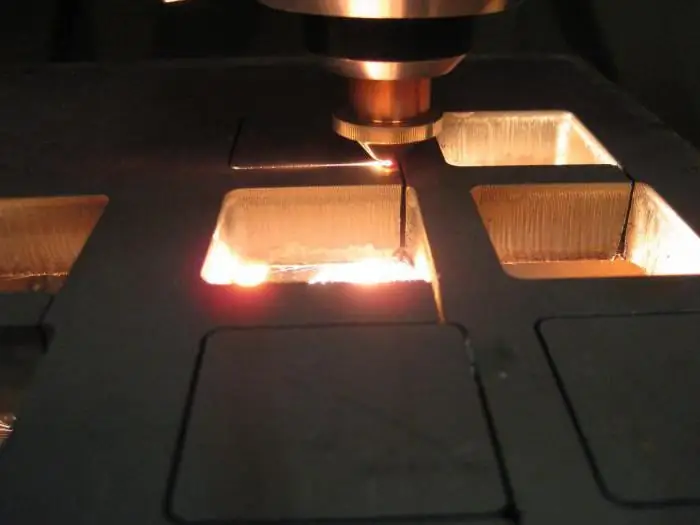
Os lasers de fibra são compactos e robustos, apontam com precisão e dissipam a energia térmica com facilidade. Eles vêm em muitas formas e, tendo muito em comum com outros tipos de geradores quânticos ópticos, têm suas próprias vantagens únicas
440 aço - aço inoxidável. Aço 440: características
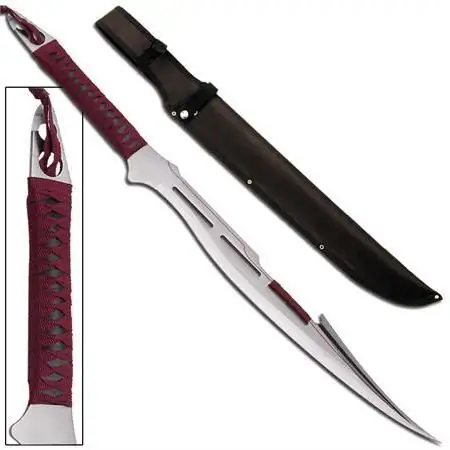
Muitas pessoas conhecem o aço 440. Ele se estabeleceu como um material duro confiável, anticorrosivo e testado ao longo do tempo, que é mais frequentemente usado para a fabricação de facas para vários fins. Qual é o segredo desta liga? Quais são suas características químicas, físicas e aplicações?