2025 Autor: Howard Calhoun | [email protected]. Última modificação: 2025-01-24 13:23
O uso de modelos de investimento é um método bastante popular de produção de fundição. O método se distingue pela complexidade do processo tecnológico e altos custos de mão de obra para processos preparatórios. Portanto, é usado onde é necessário observar com precisão as dimensões e garantir alta qualidade da superfície das peças. É assim que são fundidas lâminas de turbinas e ferramentas de alta performance, dentaduras e joias, além de esculturas de configuração complexa. A essência da fundição por cera perdida é que o molde para fundição é de uma peça, o modelo de materiais de baixo ponto de fusão não é removido durante a moldagem, mas é derretido. Isso garante a observância cuidadosa das dimensões e do relevo. O metal é derramado na cavidade remanescente do modelo. Após a conclusão do resfriamento, o molde é destruído e o produto é removido. Ao lançar grandes séries, o custo do produto é reduzido.
Benefícios do método
A principal vantagem da microfusão é a precisão da transferência do molde e a baixa rugosidade da superfície. Além disso, outros benefícios estão disponíveis:
- Produção de peças de liga leve usinadas disponíveis.
- Reduz a necessidade de usinagem adicional.
- São fundidos produtos que, de outra forma, teriam que ser feitos em partes e montados juntos.
- Com grandes séries, consegue-se uma redução na intensidade de mão de obra específica (por um produto) e seu custo.
- Possibilidade de mecanização e automatização parcial das operações preparatórias da própria fundição.
Essas vantagens tornam o método um dos mais populares e usados na metalurgia atual, especialmente em combinação com métodos modernos de fundição progressiva.
Desvantagens da fundição de investimento
As vantagens indubitáveis do método, ao que parece, deveriam ter assegurado seu domínio entre outros métodos. No entanto, apesar da popularidade do método de microfusão, desvantagens impediram sua ampla adoção. A principal desvantagem é a complexidade do processo de vários estágios. Requer equipamentos tecnológicos bastante complexos e caros para as etapas preparatórias. Para produtos simples produzidos em pequenos lotes, este método tem um custo maior.
Para a aplicação econômica de microfusão, as vantagens e desvantagens do método são comparadas, a decisão sobrea sua escolha é feita com base numa avaliação da relação preço/qualidade. Portanto, é usado principalmente para os produtos mais críticos e caros que são difíceis de obter de qualquer outra forma, como pás de turbinas, esculturas, ferramentas de alta velocidade, etc. em que o efeito de escala permite obter uma redução significativa de custos.
Tecnologia
A tecnologia de fundição por investimento é um processo de fabricação de vários estágios que é relativamente trabalhoso. Na primeira etapa, é feito um modelo mestre, que se tornará o padrão para a fabricação de modelos de trabalho após passar por todas as etapas do produto final. Para a produção de um modelo mestre, são utilizadas composições de modelos especiais e tradicionais - gesso ou madeira. O material do modelo mestre deve combinar resistência e facilidade de processamento.
Além disso, a tecnologia de microfusão prevê a criação de um molde no qual todos os modelos de trabalho serão fundidos. Os moldes são feitos de gesso, borracha, silicone, menos frequentemente de metal. Estruturalmente, deve necessariamente ser destacável e projetado para uso repetido. O molde é preenchido com uma composição de modelo, depois de endurecido, é desmontado e o próximo modelo de trabalho é removido.
Ao produzir peças únicas ou pequenas tiragens, as etapas de criação de um layout mestre e um molde são ignoradas, e um layout (ou vários) é feito moldando o material manualmente.
O próximo passo no processo de microfusão éfabricação em torno do layout (ou bloco de layouts) do molde de fundição. Estas matrizes já são estruturalmente inseparáveis e descartáveis, o que permite uma observância cuidadosa das dimensões e rugosidade do produto. Na indústria moderna, são usados dois tipos de moldes - moldes tradicionais de areia-argila para fundição no solo e moldes de concha - para a produção de peças precisas e caras.
Depois que o molde é concluído, o modelo é fundido a partir dele por aquecimento ou sopro com vapor superaquecido. As formas da casca são reforçadas adicionalmente aquecendo até 1000 ˚С.
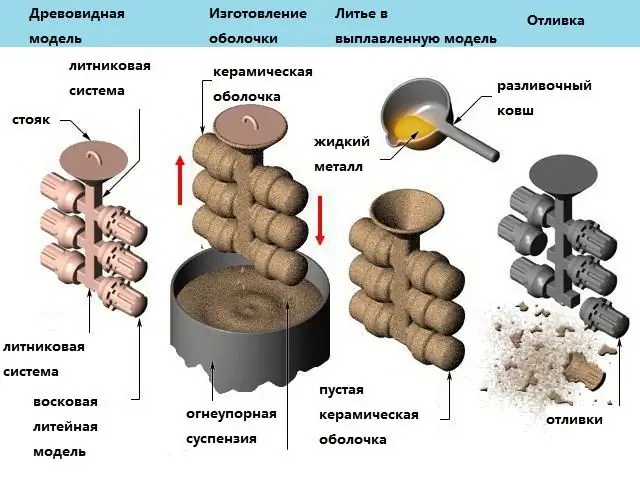
A etapa final do processo inclui a concretagem do produto, seu resfriamento em condições naturais ou por método especial em termostato, destruição do molde e limpeza do produto. O método permite obter peças fundidas de alta qualidade com peso de vários gramas a dezenas de quilogramas.
Alinhamento de modelos
O material para a confecção do layout deve possuir determinadas propriedades. Deve ter propriedades como:
- Plasticidade na fase sólida. É necessário repetir com precisão a forma do produto futuro e corrigi-lo se necessário.
- Força. O modelo deve suportar sem deformação o processo de formação de uma forma ao seu redor.
- Fusível. Renderizar um modelo não deve exigir muito tempo e energia.
- Fluidez fundida. A composição deve penetrar facilmente em todas as reentrâncias e detalhes do relevo, repetindo exatamente os contornos do detalhe futuro.
- Economia. Particularmente importante para grandes produções em série.
Para composições de modelos, geralmente é usada uma mistura de estearina e parafina. Esses materiais complementam com sucesso os parâmetros uns dos outros, compensando o ponto de fusão insuficiente da parafina e a viscosidade excessiva da estearina.
As composições à base de cera de lignite não são menos populares na indústria. Suas principais propriedades são a resistência à umidade, resistência e a capacidade de formar revestimentos muito lisos, o que é especialmente valioso para a modelagem de produtos.
Compostos que consistem em uma mistura de cera de carvão marrom, parafina e estearina também são usados.
Fabricação de moldes
Para a produção de produtos exclusivos, um layout é elaborado recortando um pedaço de material de modelo manualmente ou de acordo com modelos. Modelos na forma de corpos de revolução também são feitos em tornos. Recentemente, o método de impressão 3D de modelos tornou-se cada vez mais difundido. É adequado tanto para layouts simples quanto para pequenas séries.
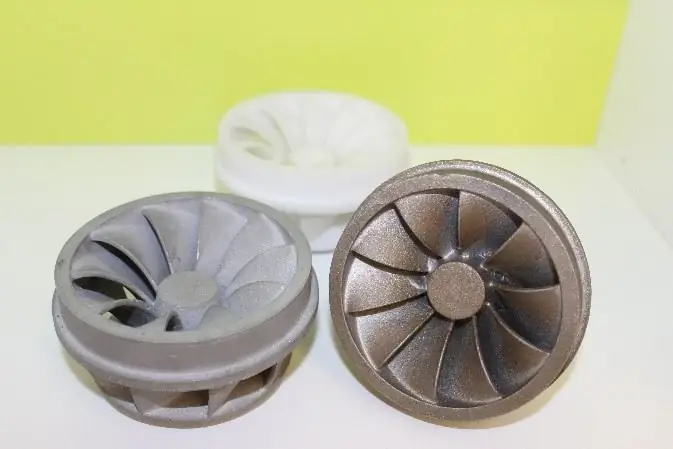
O custo de uma impressora 3D industrial moderna ainda é alto, mas devido à facilidade de reconfiguração de um produto para outro, ela pode se tornar uma ferramenta eficaz de modelagem no caso de um grande número de pedidos heterogêneos de pequenas séries.
Para fazer um grande número de layouts idênticos, uma matriz é feita de gesso, borracha, silicone ou metal. Os layouts de trabalho são produzidos, por sua vez, por lançamento em uma matriz. Por projeto, o molde deve ser desmontável para garantir a possibilidade de fabricação de um determinado número de modelos. O material selecionado também deve proporcionar tal oportunidade, portanto, são impostos a ele requisitos como resistência, densidade, baixa rugosidade e inércia química em relação ao layout. A substância do molde também deve ter uma adesão mínima à maquete para garantir que as maquetes acabadas possam ser facilmente removidas e as dimensões aderidas. Uma propriedade importante do molde é sua resistência e resistência ao desgaste, especialmente para grandes séries.
Fazendo modelos e blocos
Um método amplamente utilizado de fabricação de modelos de investimento é lançá-los sob baixa pressão em moldes. A injeção da mistura líquida é realizada tanto manualmente, por meio de seringas de pistão, quanto por compressores mecânicos, hidráulicos ou pneumáticos. No caso de utilização de cera de lenhite, é necessário aquecer as tubulações para fornecimento da composição devido à sua alta viscosidade. Os modelos de poliestireno expandido são feitos por extrusão em máquinas de moldagem automatizadas.
Para aumentar a eficiência econômica e reduzir a intensidade de mão de obra no caso de produção em série de pequenas peças fundidas, seus layouts são combinados em blocos. Os sistemas de gating são formados acima dos blocos anexando layouts individuais aos sprues usando um ferro de solda manual. No caso de peças fundidas avulsas ou pequenas séries, os modelos são feitos à mão.
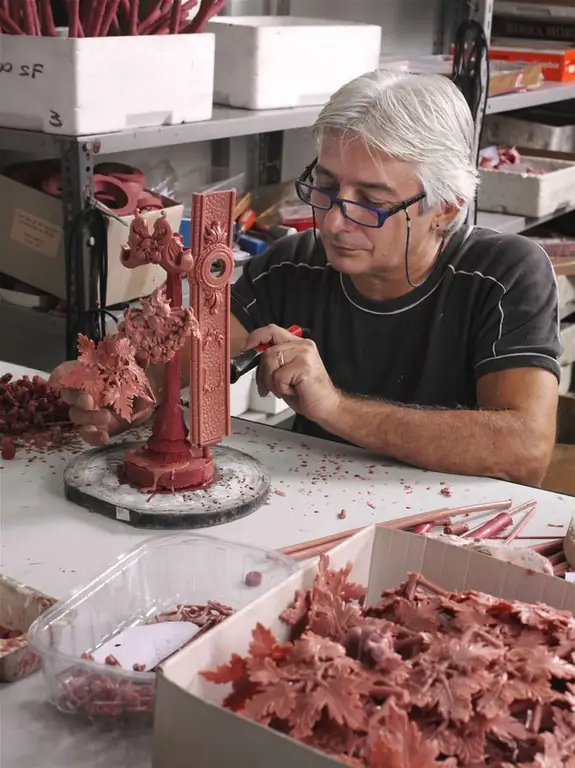
Ao formar sistemas de gating, é necessário garantir um fluxo não turbulento do fundido, preenchimento uniforme de todos os elementos da matriz. Ao preencher um formulário do PGS, você também deve monitorar o preenchimento uniforme de todos osaberturas entre os sprues e evitando danos.
Fazendo um molde
No método de microfusão em consideração, existem dois tipos principais de moldes:
- Misturas de areia e argila (SGM).
- Shell.
Os moldes de fundição de cera fluída são usados principalmente na produção de pequenas séries de produtos que não exigem precisão muito alta. O processo de sua fabricação é bastante trabalhoso e requer habilidades altas e muitas vezes únicas de modeladores e moldadores. A mecanização parcial se presta apenas a certas operações, como preparar e encher a areia de moldagem, sua compactação.
Os moldes de casca, por outro lado, são usados para produzir peças que requerem precisão especial de fabricação. O processo de fabricação é mais complexo e demorado, mas se presta melhor à mecanização.
Fundição no solo
Este é o método mais antigo de processamento de metal dominado pela humanidade. Foi dominado por nossos ancestrais simultaneamente com o início do uso de produtos metálicos como armas, ferramentas ou utensílios, ou seja, há cerca de 5 mil anos. O metal fundido é derramado em uma matriz preparada a partir de uma mistura de areia e argila. Os primeiros lugares para o processamento de metais surgiram onde os depósitos de metais na forma de pepitas e colocadores estavam localizados nas proximidades. Um exemplo típico é a fábrica de Kasli nos Urais, mundialmente famosa por sua fundição de renda de ferro.
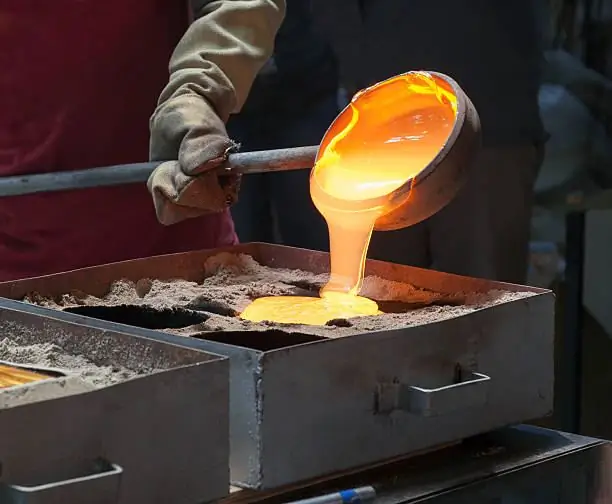
O método de microfusão é utilizado para a fabricação de produtos metálicos - ferrosos ecolori. E apenas para metais que apresentam uma tendência aumentada de reagir na fase líquida (como o titânio), é necessário fazer matrizes de outras composições.
O processo de produção de fundição em PGS consiste nas seguintes fases:
- modelagem;
- preparando o frasco;
- enchimento e compactação da mistura no frasco;
- fundição de metal;
- removendo e limpando a carcaça.
Formulário de ASG - uso único. Para obter o produto acabado, ele terá que ser quebrado. Ao mesmo tempo, a maior parte da mistura está disponível para reutilização.
Composições de areias predominantemente quartzosas de vários tamanhos de grão e argilas plásticas, cujo teor varia de 3 a 45 por cento, são usadas como materiais para ASG. Assim, por exemplo, as peças fundidas artísticas são produzidas usando uma mistura com um teor de argila de 10-20%, para peças vazadas especialmente grandes, o teor de argila é ajustado para 25%.
Dois subtipos são usados:
- Revestimento de misturas. Eles estão localizados na superfície interna do molde e interagem com o metal fundido. Eles devem ser resistentes ao calor, capazes de não serem destruídos por diferenças de temperatura e tensões resultantes. Estas misturas têm um grão fino para transmitir cuidadosamente os detalhes da superfície. A capacidade da mistura de passar gás também é muito significativa.
- Misturas de recheio. Eles são usados para preenchimento entre a camada de revestimento e as paredes do frasco. Eles devem suportar o peso do metal vazado, manter a forma do produto e contribuir para a remoção oportuna e completa dos gases. Produzido a partir de graus mais baratos de areia,reutilizável.
Se os gases de fundição não escapam pelas massas de areia de moldagem, mas pelo sistema de gating, ocorrem defeitos na fundição, levando ao casamento.
A tecnologia tradicional de fundição no solo é ilustrada em detalhes no filme "Andrei Rublev" de A. Tarkovsky. No conto "O Sino", o jovem Boriska, filho de um mestre falecido, chefia um artel de fundição e lança um sino de igreja.
Carcaça de casco
O método de microfusão em moldes shell é caracterizado pela melhor transferência das dimensões do produto e baixa rugosidade superficial. O modelo é feito de compostos fusíveis, como cera de carvão marrom. As fundições também usam amplamente a composição de parafina-estearina em proporções iguais. No caso de peças fundidas de grandes dimensões, os sais são incluídos no material do modelo para proteger o modelo contra deformações. Ao mergulhar na solução, o modelo é coberto em 6-10 camadas com uma suspensão de alta temperatura.
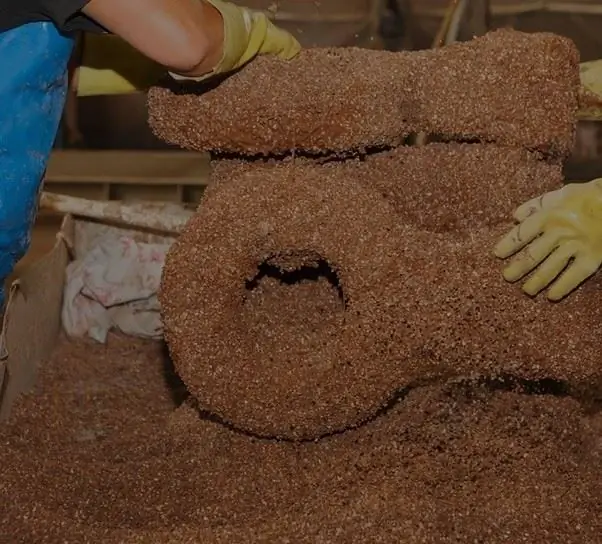
Os silicatos hidrolisados atuam como aglutinantes, os cristais de eletrocorindo ou quartzo são tomados como uma aspersão resistente ao calor. Os materiais do molde Shell são caracterizados por alta resistência, baixa higroscopicidade e excelente permeabilidade ao gás.
O layout é seco em uma atmosfera de amônia gasosa. Na próxima etapa, o molde é aquecido a 120 ˚C para remover o modelo de parafina. Os restos da mistura são removidos com vapor superaquecido sob alta pressão. Em seguida, o molde é calcinado a temperaturas de até 1000 ˚С, o que leva à sua fixação final e remoção de substâncias,que podem ser liberados como gases durante o processo de fundição.
A concha é colocada em uma espécie de frasco, que é coberto com granalha de aço. Isso ajuda a manter a configuração ao encher o molde com material fundido e, ao mesmo tempo, melhora as condições de resfriamento do fundido. O fundido é derramado em moldes aquecidos a 1000 ˚С. Após o resfriamento do produto de acordo com um programa especial em um termostato, o molde é destruído, a fundição é removida e limpa.
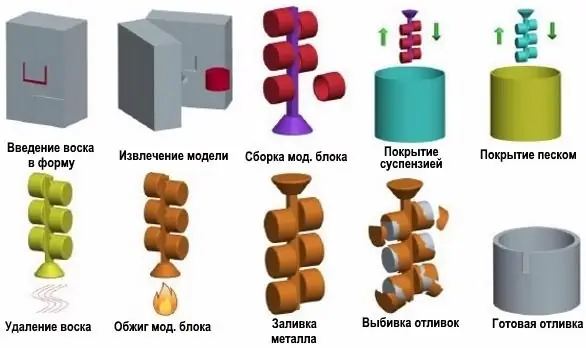
A principal vantagem deste método de fundição é a alta precisão dimensional e baixa rugosidade da superfície.
Vantagens adicionais do método:
- Fundição de peças de ligas difíceis de usinar.
- Fundição de itens que, de outra forma, teriam que ser moldados aos poucos e depois reunidos novamente.
As desvantagens deste método de microfusão são a baixa utilização de metal e o aumento da intensidade de trabalho.
Fundição de precisão
Fundição de precisão - este é o nome dado tanto à tecnologia quanto ao próprio produto final. A alta precisão da fundição é garantida pelo fato de que durante a preparação do molde não há necessidade de extrair o modelo do produto dele. Ao usar o método tradicional, a produção de uma matriz de fundição é um processo de várias etapas complexo e muito demorado. Isto é especialmente verdadeiro no caso de peças fundidas de configuração complexa, com reentrâncias, depressões e cavidades internas.
Por exemplo, ao fundir um vaso de ferro fundido ou cobre com uma curvatura de superfície variável, você tem que usar muitos truques. Sim, primeiroa metade inferior do frasco é enchida, depois o modelo é removido, virado e a metade superior é compactada. O modelo tem que ser composto, as alças do vaso são feitas de dois elementos, eles são puxados através da cavidade do modelo em duas etapas - primeiro o elemento inferior, depois o superior. Todas essas inúmeras voltas e arrastes não podem ter um efeito positivo na integridade da superfície do molde e, em última análise, na precisão de manter as dimensões do fundido e a qualidade de sua superfície. Além disso, permanece o problema de combinar com precisão as partes dos frascos e prendê-los com segurança uns aos outros.
A produção de microfusão é desprovida dessas deficiências, não requer modeladores altamente qualificados e reduz significativamente a intensidade de mão de obra das operações de pré-fundição. Isso é especialmente pronunciado com grandes séries de peças fundidas.
O método permite atingir a 2-5ª classe de precisão de acordo com GOST 26645-85. Isso possibilita a fundição de produtos de alta precisão, como lâminas de turbina, ferramentas de corte, incluindo fresas e brocas de alto desempenho, suportes críticos de alta carga, pequenas peças de veículos de alta carga, máquinas-ferramentas e outros mecanismos complexos.
Alta precisão dimensional e alta classe de superfície minimizam a necessidade de usinagem adicional da fundição, o que economiza metal e reduz os custos de produção.
Equipamento
Os equipamentos de microfusão necessários são variados e complexos. As empresas os combinam em um complexo único e bem coordenado,organizado como um site, oficina ou produção separada.
A composição do complexo depende da escala de produção, tamanho, configuração e circulação dos fundidos.
Assim, na produção de próteses e bijuterias, os equipamentos incluirão:
- tabela modelo;
- forno mufla com termostato;
- um conjunto de bisturis e espátulas para corrigir a forma do modelo;
- formando placa;
- frasco;
- tanques para armazenamento e preparo de areia de moldagem;
- conjunto de ferramentas de compactador de areia;
- cadinho para derretimento de metal;
- fórceps;
- martelo para quebrar o molde.
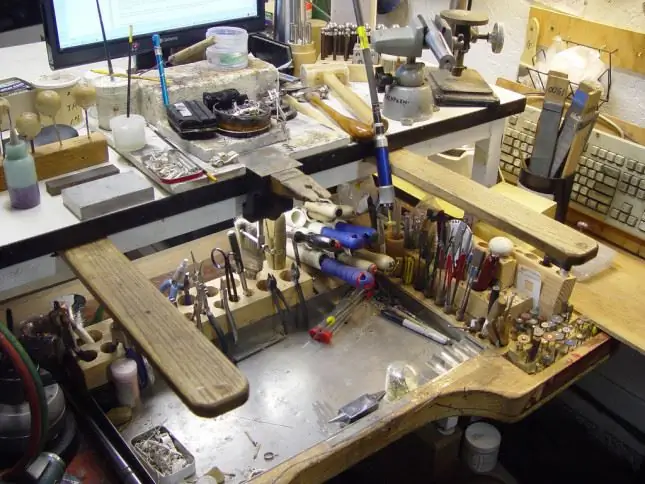
Este complexo de produção pode caber facilmente em uma mesa e em um armário. Se for planejado produzir em massa, por exemplo, peças fundidas de alumínio - partes de um dispositivo, serão necessários equipamentos para:
- moldar e vazar moldes de cerâmica;
- formas de secagem;
- derreter o material do modelo e aplicar uma camada resistente ao calor;
- limpeza de peças fundidas do material de moldagem.
E, finalmente, o próprio equipamento do complexo de fundição, projetado para obter um fundido e despejá-lo em um molde. Pode ser equipamento de fundição:
- sob baixa pressão;
- centrífuga;
- na forma usual da gravidade.
Máquinas de moldagem por injeção e fundição centrífuga são separadas altamente mecanizadas e automatizadascomplexo de produção, isolado da atmosfera da loja. Eles minimizam o trabalho manual e a exposição humana a condições prejudiciais. As câmaras seladas nas quais os complexos estão localizados proporcionam a completa captura e purificação dos gases de exaustão, o que aumenta significativamente a compatibilidade ambiental do empreendimento.
A fundição por cera perdida tem um potencial bastante alto para desenvolvimento, especialmente quando combinada com técnicas avançadas de fabricação e vazamento de moldes.
Recomendado:
Fundição contínua de aço: princípio de funcionamento, equipamentos necessários, vantagens e desvantagens do método
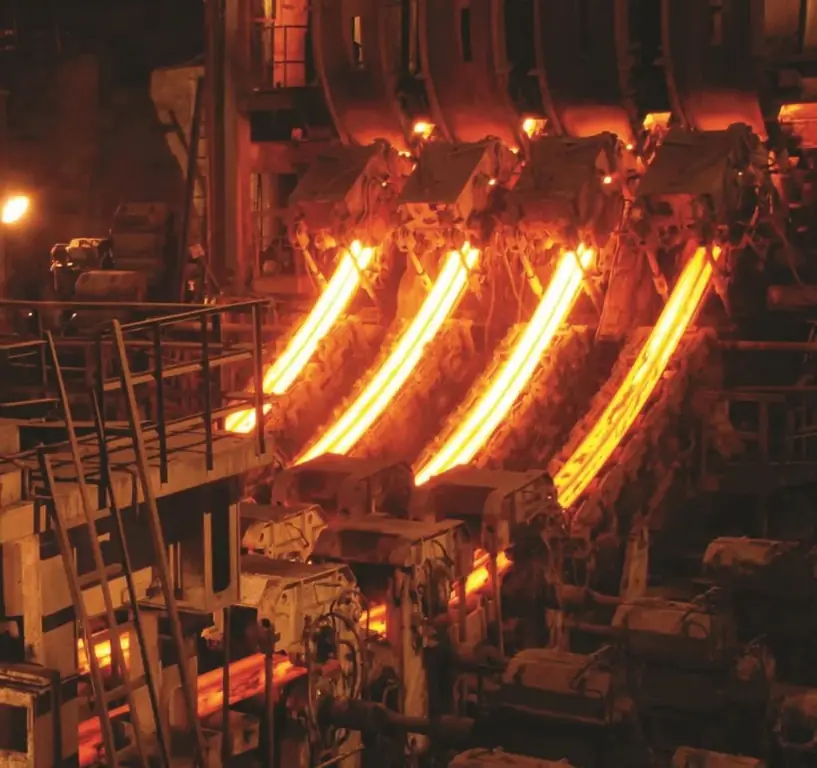
Hoje, um grande número de várias coisas, peças, etc. são feitos de aço. Naturalmente, isso requer uma grande quantidade de material de origem. Portanto, as usinas há muito usam o método de lingotamento contínuo de aço, caracterizado pela característica mais importante - alta produtividade
Gravação em plexiglas: vantagens e desvantagens, tecnologia, equipamentos
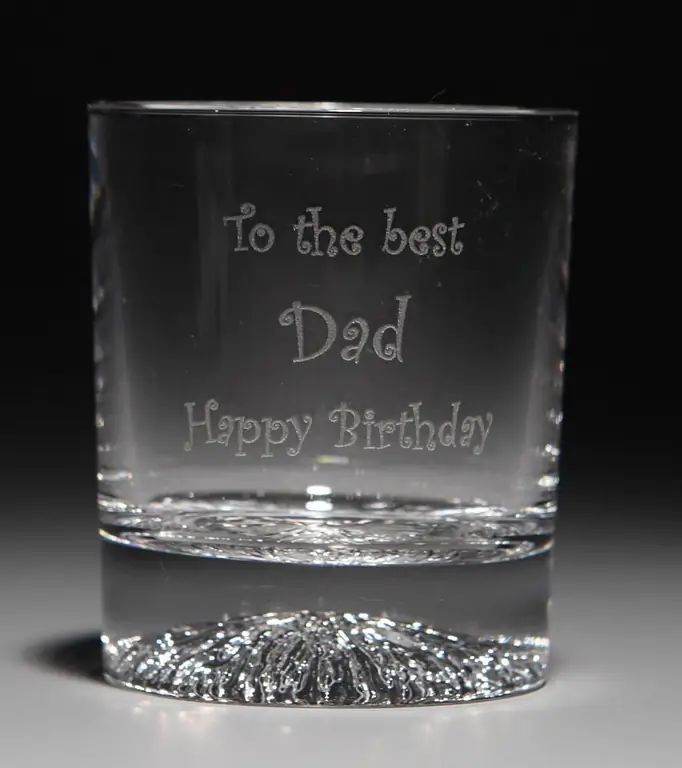
Gravura em plexiglas é considerada um ofício de pintura. Uma estatueta de lembrança, vitrais ou uma mesa de vidro, decorada com desenhos requintados, incorporam um delicado gosto artístico. As tecnologias de decapagem e jateamento de areia estão no passado. Hoje, com a ajuda de uma máquina a laser, cada pessoa pode criar um padrão altamente detalhado
Letterpress é Tecnologia de impressão tipográfica, modernos estágios de desenvolvimento, equipamentos necessários, vantagens e desvantagens deste tipo de impressão
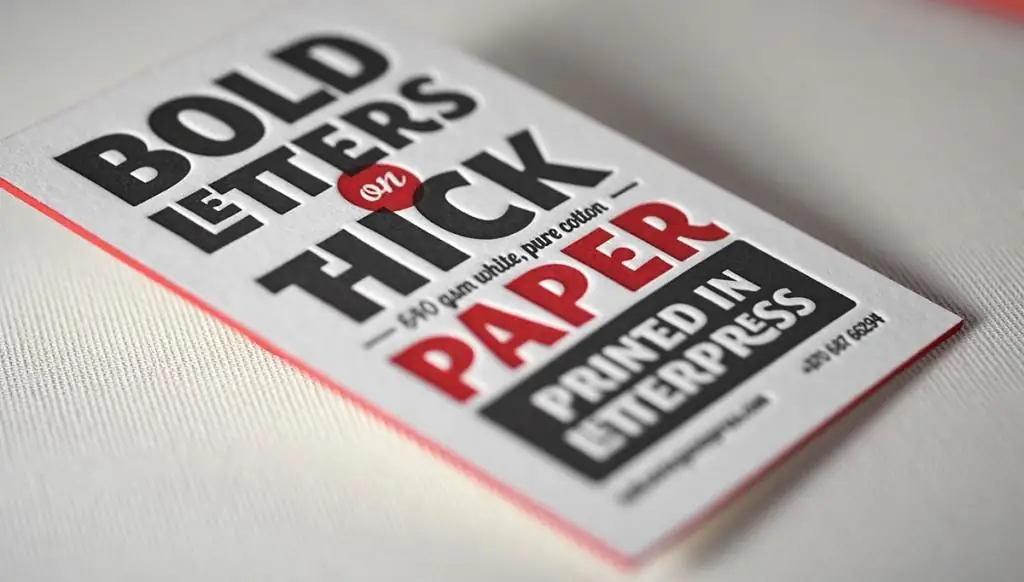
A tipografia é um dos métodos típicos de aplicação de informações usando uma matriz de relevo. Os elementos que se projetam são cobertos com tinta na forma de uma pasta e depois pressionados contra o papel. Assim, vários periódicos de massa, livros de referência, livros e jornais são replicados
Processamento ultrassônico: tecnologia, vantagens e desvantagens
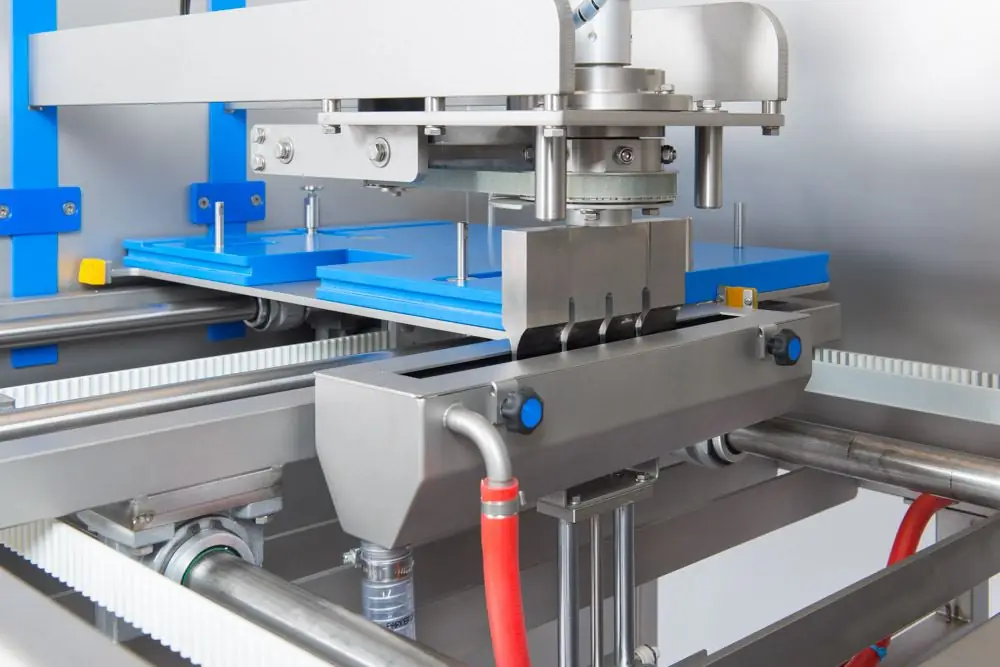
A indústria metalúrgica nesta fase de desenvolvimento é capaz de resolver as complexas tarefas de corte e furação de peças de vários graus de dureza. Isso se tornou possível devido ao desenvolvimento de formas fundamentalmente novas de influenciar o material, incluindo um amplo grupo de métodos eletromecânicos. Uma das tecnologias mais eficazes desse tipo é o tratamento ultrassônico (UZO), baseado nos princípios da radiação eletroacústica
Fundição em molde de silicone: equipamento. Fundição a vácuo em moldes de silicone
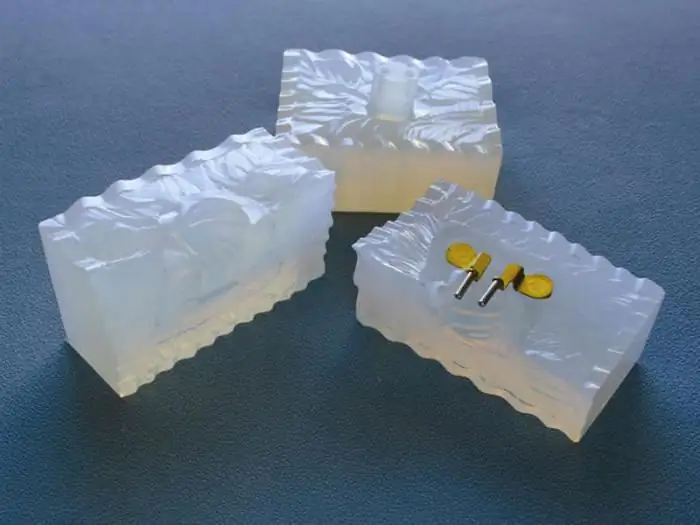
Para a fabricação de um pequeno número de blanks de plástico, a fundição a vácuo em moldes de silicone é mais usada. Este método é bastante econômico (fazer um molde de metal requer mais tempo e dinheiro). Além disso, os moldes de silicone são usados repetidamente, o que também reduz significativamente o custo de produção