2025 Autor: Howard Calhoun | [email protected]. Última modificação: 2025-01-24 13:23
A qualidade da soldagem é determinada pela resistência da costura. Ao mesmo tempo, o controle de conexão deve ser não destrutivo, o que força os mestres a recorrer a métodos especiais de verificação após a conclusão da operação. Em alguns casos, a inspeção externa sem instrumentos também é permitida, mas no caso de estruturas críticas, a inspeção visual não pode ser limitada. Ele pode ser complementado pela detecção de falhas de cor de soldas - um dos métodos mais eficazes, convenientes e confiáveis para analisar essas juntas.

Recursos do método de verificação
Este método de verificação de soldas refere-se ao capilar, mas se concentra apenas na solução de problemas externos. Ou seja, não pode ser usado para verificar a estrutura interna da zona da junta, em contraste, por exemplo, com a detecção de falhas ultrassônicas. Normalmente, os metais propensos a rachaduras são submetidos a tais testes. Além disso, o controle de cores permite identificar de forma eficaz as descontinuidades que vêm à tona.
Quanto ao princípio de verificação, baseia-se na sensibilidade dos metais à interação com materiais não ferrosos não defectoscópicos. Ao contrário da crença popular, a análise comoinformações controladas não usam as características da superfície da peça, mas as alterações provocadas pela irritação da estrutura com produtos químicos. O método de detecção de falhas de cor é baseado nos processos de exposição química, o que permite processar informações sobre alterações e fornecer dados sobre as falhas de metal identificadas na saída.
O método em si raramente é usado sozinho. Geralmente é usado no complexo de verificação geral - junto com o ultra-som. A análise de cor segue primeiro, seguida pelo teste ultrassônico.
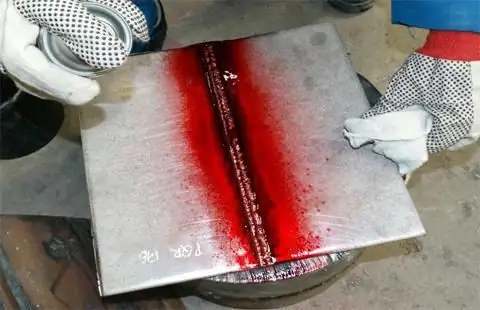
Materiais aplicados
Como já mencionado, a detecção de falhas não é completa sem o uso de produtos químicos especiais. O kit padrão para detecção de falhas de cor inclui três tipos de componentes: penetrante indicador, agente de limpeza e revelador. Ou seja, o controle de sensibilidade de cor será ativado pelo processamento em três estágios da área de trabalho. Materiais especiais são usados em cada etapa.
Penetrantes são, na verdade, substâncias corantes que podem se apresentar em diferentes formas. Produtos em pó também são usados, mas operações adicionais de ação térmica ou mistura com líquidos devem ser introduzidas para seu uso. Penetrantes adequados para um metal específico para detecção de defeitos não ferrosos são selecionados com base em várias propriedades de desempenho. Leva em consideração, em particular, a resistência ao fogo, respeito ao meio ambiente e toxicidade, a eliminação da necessidade de decapagem posterior, etc.
Requisitos paralocal de controle
A operação de detecção de falhas só pode ser realizada em uma sala especialmente preparada. É importante levar em consideração os requisitos para os equipamentos de comunicação do local, para características do ar, suporte técnico, etc. A sala deve ser ventilada, não ter fontes de chama aberta ou calor intenso. A iluminação deve ser geral e local, as lâmpadas próximas ao local de operação devem ser protegidas dos efeitos térmicos.
Você deve inicialmente cuidar da criação de um microclima ideal - somente em condições favoráveis, a detecção de falhas de cor de qualidade pode ser realizada. GOST 18442-80, em particular, indica que o ar deve estar seco e quente - se necessário, para atingir essas características, você pode usar um aquecedor infravermelho que secará o revelador a um nível de 5 ° C. O equipamento técnico dependerá dos métodos de aplicação dos componentes químicos. Em particular, pistolas de pulverização, latas de aerossol, escovas, etc. podem ser usadas para aplicar o mesmo penetrante.
Preparando a costura da base
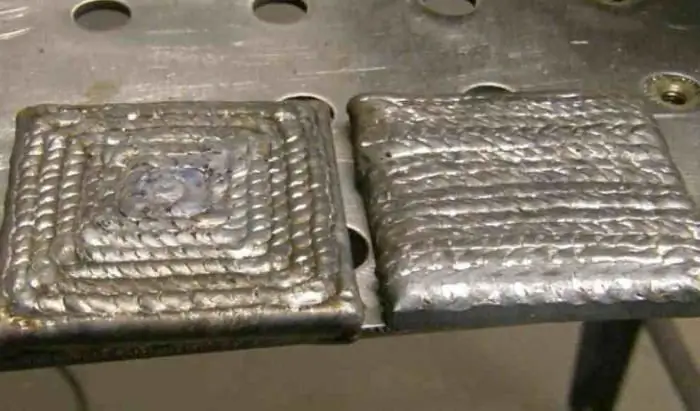
A seção de conexão também está sendo preparada para a operação de detecção de falhas. Se houver rugosidade ou contaminação pronunciada na superfície, você poderá usar material de granulação fina e fazer um processamento leve. Em seguida é o desengorduramento. Para esta tarefa, um dos componentes do kit de detecção de defeitos pode ser utilizado, mas é importante que ele proporcione o efeito desengordurante e, melhor ainda, aumentesensibilidade de controle. Não é recomendado o uso de querosene para tais fins, mas pode-se usar gasolina e acetona. Se não houver ventilação na sala, o desengorduramento é realizado apenas com soluções aquosas à base de agentes sintéticos em pó de baixa concentração. Se a detecção de falhas de cor de uma pequena peça for planejada, a imersão total em uma composição desengordurante também pode ser usada. Em outros casos, é utilizada a técnica de pulverização na área alvo ou aplicação com um pano embebido na solução.
Aplicar penetrante
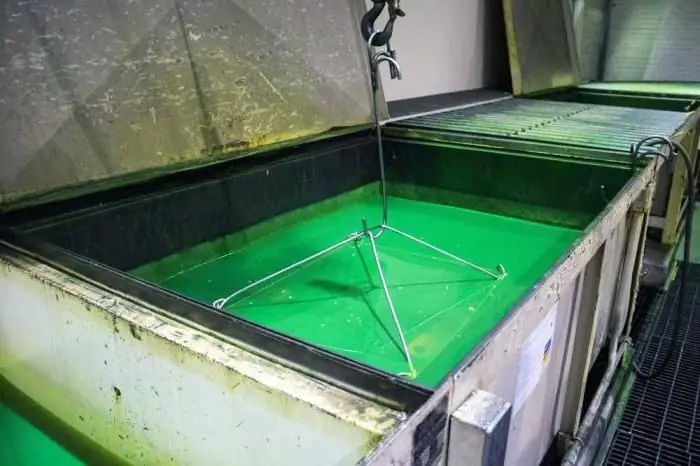
Primeiro de tudo, o penetrante indicador é aplicado. Tal como acontece com o desengorduramento, este procedimento pode ser realizado por pulverização, imersão ou escovagem, dependendo das características da peça. Além disso, a aplicação deve ser feita em várias camadas (4-6) e para que cada camada anterior da composição não tenha tempo de secar. Além disso, para que a detecção de falhas de cor nas soldas mostre um resultado otimamente preciso, cada camada subsequente deve cobrir uma área maior em relação à anterior. Isso se deve ao fato de que cada nova camada irá dissolver o contorno da mancha anterior, evitando transições acentuadas e flacidez, que podem ser percebidas como falsas trincas. Se a operação for realizada em condições de temperatura negativa, o próprio penetrante deve ter um estado de cerca de 15 ° C.
Remoção penetrante
Imediatamente após a aplicação, o filme indicador deve ser removido com um pano limpo oupilha. O material deve primeiro ser umedecido com álcool etílico e a superfície limpa até que o revestimento seja completamente eliminado. Podem surgir problemas se o trabalho for realizado na superfície de um metal áspero - neste caso, faz sentido usar abrasivos leves. Em seguida, é aplicada uma mistura de óleo-querosene. Cobre toda a área-alvo e, em seguida, também é removido com trapos ou guardanapos. Durante as duas etapas descritas, a detecção de falhas de cor deve manter a superfície limpa e seca ao redor da costura. Isso é importante para manter a precisão dos procedimentos de controle adicionais.
Aplicar desenvolvedor
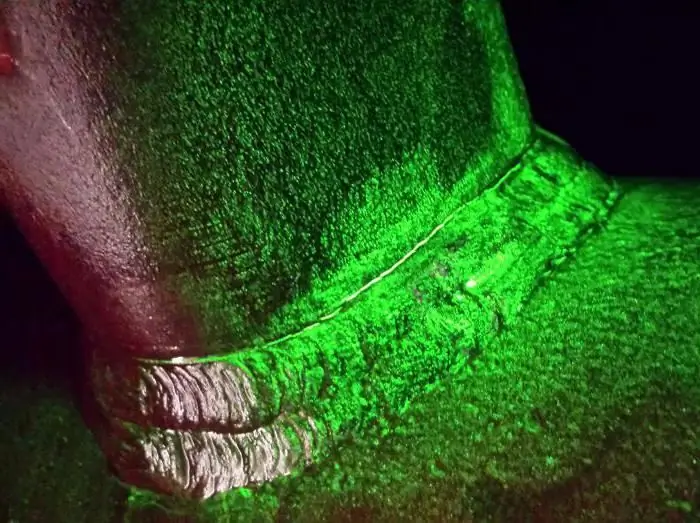
Assim como as camadas indicadoras e limpadores, o revelador é aplicado de várias maneiras, de pincéis a pistolas de pulverização. O principal nesta fase é observar a uniformidade e a solidez do revestimento formado. Portanto, é necessário verificar cuidadosamente as ferramentas de pulverização, bicos e outros elementos dos dispositivos que afetam a qualidade da entrega do produto ao local de destino. Tudo isso afetará ainda mais o controle da detecção de falhas de cor, bem como a qualidade das operações de verificação subsequentes. A secagem é realizada após a aplicação do revelador. Não pode ser realizada, aguardando a polimerização em condições naturais, mas para agilizar o processo, é permitido o uso de aquecedores de ponto de baixa potência.
Inspeção da área controlada
Quando o revelador estiver seco, você pode se preparar para inspecioná-lo esperando mais 30 minutos ou mais. O controle adicional pelo método de detecção de falhas de cor envolve o uso de uma lupa,proporcionando uma ampliação mínima de 5x. Se for usada a técnica camada por camada, o teste pode ser realizado em até 2 minutos após o processamento com o revelador.
Durante o processo de avaliação, o operador captura as características da mancha deixada - em particular, registra as dimensões dos contornos, forma, etc. A principal tarefa da detecção de falhas de cor é detectar falhas de superfície que se manifestam claramente após os procedimentos de conclusão. Tanto danos mecânicos quanto traços de ataque corrosivo, bem como trincas com flacidez excessiva podem ser identificados.
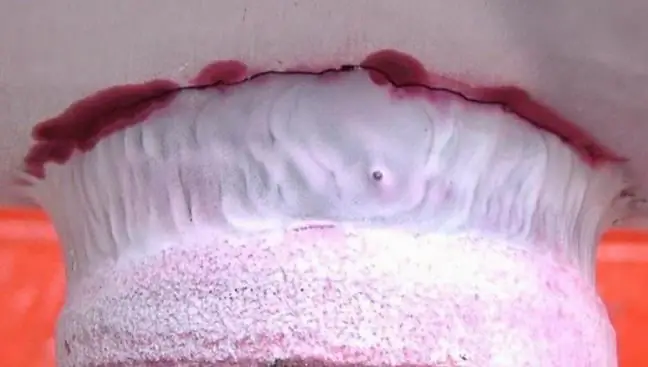
Segurança na detecção de falhas
Os requisitos para medidas de segurança são devido à ameaça de incêndio e explosão durante a detecção de falhas. Portanto, é necessário preparar pelo menos um macacão, incluindo um manto de algodão, um cocar e luvas de borracha, cuja superfície deve ser revestida com pó de talco. No próprio site, as medidas de segurança devem ser integralmente observadas. Durante o procedimento, não deve haver fontes abertas de fogo ou faíscas. Se o teste de penetrante de cor for realizado regularmente na mesma sala, devem ser instalados sinais apropriados de não fumar e de proteção contra incêndio. Panos, lenços umedecidos e produtos inflamáveis devem ser armazenados em um recipiente à prova de fogo.
Conclusão
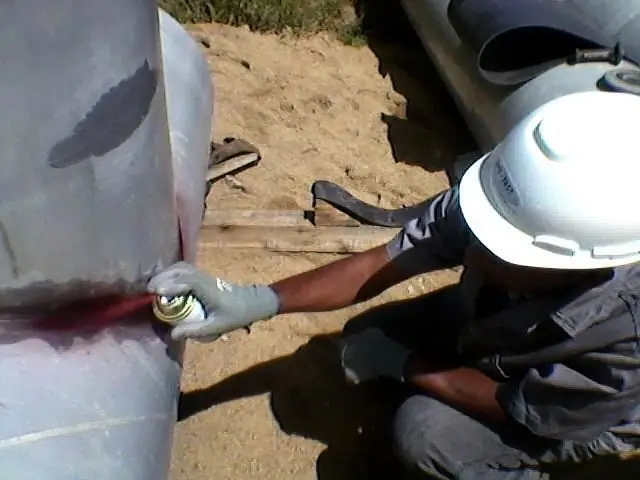
Seria errado considerar este método de avaliação da qualidade de uma soldacomo ideal, escolhendo-o da gama geral de outros métodos. Este é um método de exame especialmente direcionado, focado especificamente na análise da superfície da peça de trabalho. Ou seja, a detecção de falhas de cor não é uma medida de controle abrangente, mas fornece informações sobre falhas externas com eficiência relativamente alta. Se este método for complementado com outros métodos para estudar a estrutura interna da solda, podem ser obtidas informações completas sobre a estrutura do metal. Além disso, já está tomada uma decisão sobre a possível correção dos defeitos identificados. Em alguns casos, a soldagem secundária é realizada - isso dependerá do número e da importância dos defeitos em termos de afetar a resistência da estrutura da peça. Às vezes, a solução de problemas desse tipo também é usada para analisar a estrutura de juntas e juntas antigas em estruturas operadas.
Recomendado:
Controle visual de soldas: a essência da conduta e o passo a passo

Eliminar completamente o risco de conexões de baixa qualidade não permitem máquinas de solda automáticas e robóticas. Portanto, independentemente da tecnologia aplicada para a produção de operações de soldagem, após sua execução, é implementado um procedimento para uma verificação abrangente da qualidade das soldas. O método de inspeção visual é o estágio inicial no processo geral de solução de problemas de soldagem
Cor do cavalo marrom: descrição, história, características e fatos interessantes
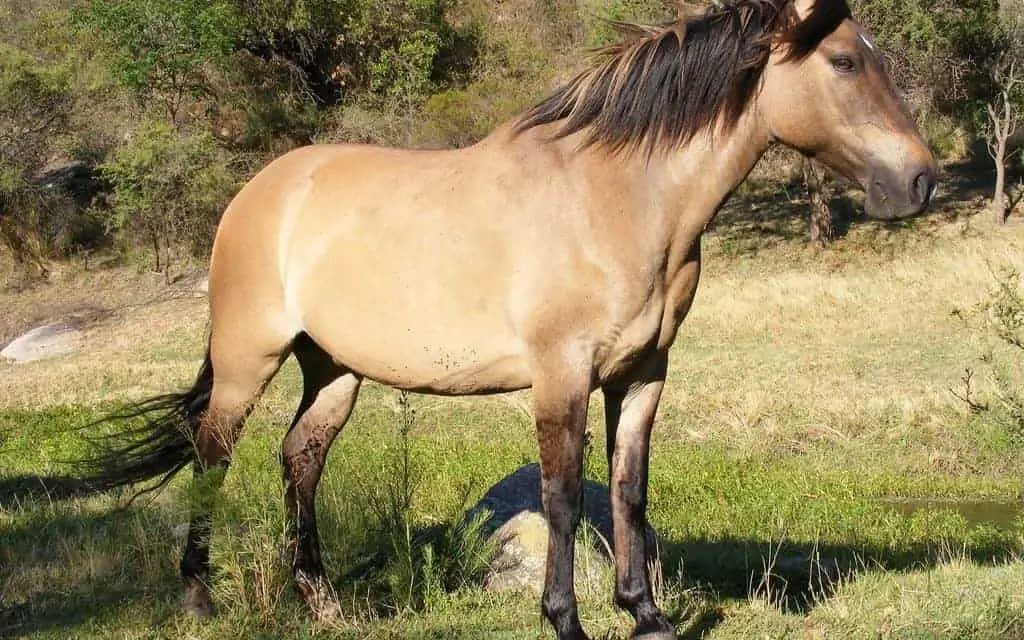
De onde veio o nome da cor do cavalo. A história da aparência da raça e alguns fatos interessantes. As principais variedades de cavalos de camurça. Várias descrições da aparência e características dos cavalos de camurça. A história dos cavalos de camurça na cultura. Confusão com outras raças
O que é exame radiográfico? Controle radiográfico de soldas. Controle radiográfico: GOST
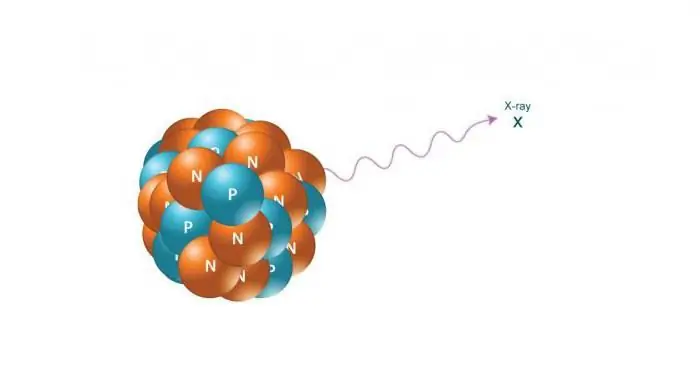
Bases físicas dos métodos de controle de radiação. Características do controle radiográfico. As principais etapas do controle radiográfico de soldas. Precauções de segurança na produção de controle radiográfico. Documentação normativa e técnica
Defeitos do pão: fotos, causas, problemas de cozimento e como corrigi-los
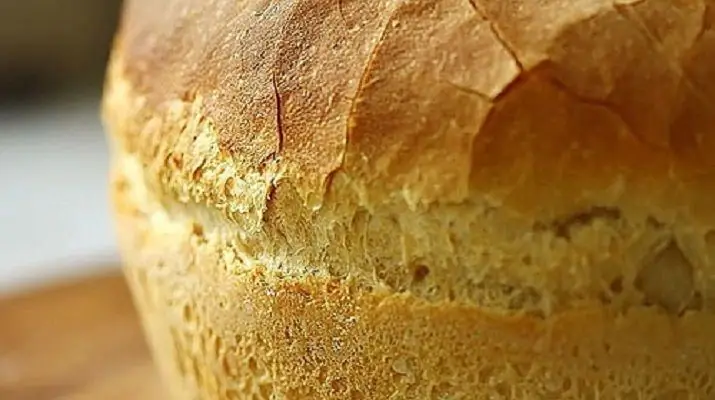
A fabricação de pão é um processo tecnológico complexo. Não surpreendentemente, os produtos de panificação acabados podem ter vários defeitos. Eles podem ser causados pela má qualidade das matérias-primas, pelos erros do padeiro que amassa a massa e assa. Vale ress altar que as falhas associadas à qualidade dos ingredientes são extremamente difíceis de corrigir, enquanto as falhas tecnológicas podem ser corrigidas. O artigo fala sobre os defeitos do pão e como eliminá-los
Defeitos da madeira: tipos, descrição e soluções
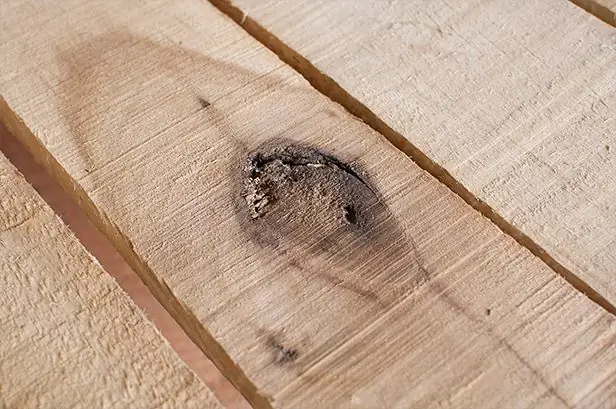
Hoje, existem muitos materiais de construção. Um dos mais antigos, mas ao mesmo tempo, a madeira se espalhou. No entanto, como se sabe, este material é "vivo" e, portanto, não é desprovido de defeitos naturais. A madeira é altamente suscetível a várias influências