2025 Autor: Howard Calhoun | [email protected]. Última modificação: 2025-06-01 07:15
A qualidade da solda é determinada não apenas pela capacidade do mestre de organizar o arco corretamente, mas também pela proteção especial da área de trabalho contra influências externas. O principal inimigo no caminho para criar uma conexão metálica forte e durável é o ambiente natural do ar. O isolamento da costura do oxigênio fornece fluxo para soldagem, mas não apenas essa é sua tarefa. Diferentes configurações da composição deste aditivo com uma combinação de ambiente de gás protetor permitem controlar os parâmetros da junta de costura de diferentes maneiras.
Atribuição de fluxo
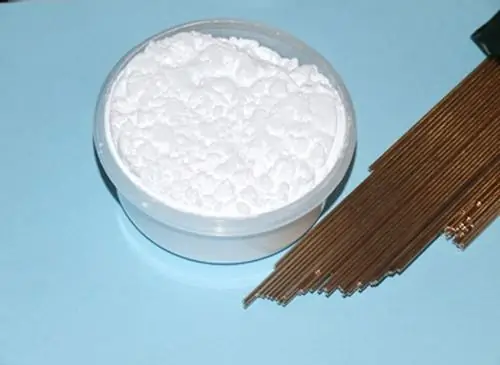
O consumível de soldagem deste tipo é enviado para a zona de combustão e, dependendo das características de seu fundido, exerce um efeito protetor e modificador na área de formação da solda. Em particular, o material pode desempenhar as seguintes funções:
- Criação de isolamento de escória e gás para a poça de fusão.
- Dando uma junta soldadacertas propriedades técnicas e físicas.
- Manter a estabilidade do arco.
- Transferência do metal do eletrodo (ou fio fundido) para a zona de soldagem.
- Remoção de impurezas indesejadas na camada de escória.
Se falamos sobre a compatibilidade de diferentes fluxos para soldagem com metais, as marcas mais comuns têm os seguintes propósitos:
- FC-9 - ligas de carbono de aço de baixa liga.
- AN-18 - ligas de aço de alta liga.
- AN-47 - aços de baixa e média liga, caracterizados por características de alta resistência.
- AN-60 - aços de baixa liga usados em tubulações.
- ФЦ-7 - usado ao soldar aço macio em alta corrente.
- FC-17 - ferro de alta temperatura centrado na face.
- FC-19 - ligas com alto teor de cromo.
- ФЦ-22 - é usado para fazer uma junta de costura de filete em trabalhos com aços carbono ligados.
- 48-OF-6 - é utilizado em técnicas de soldagem com a conexão de fio eletrodo de alta liga.
Composições de fluxo
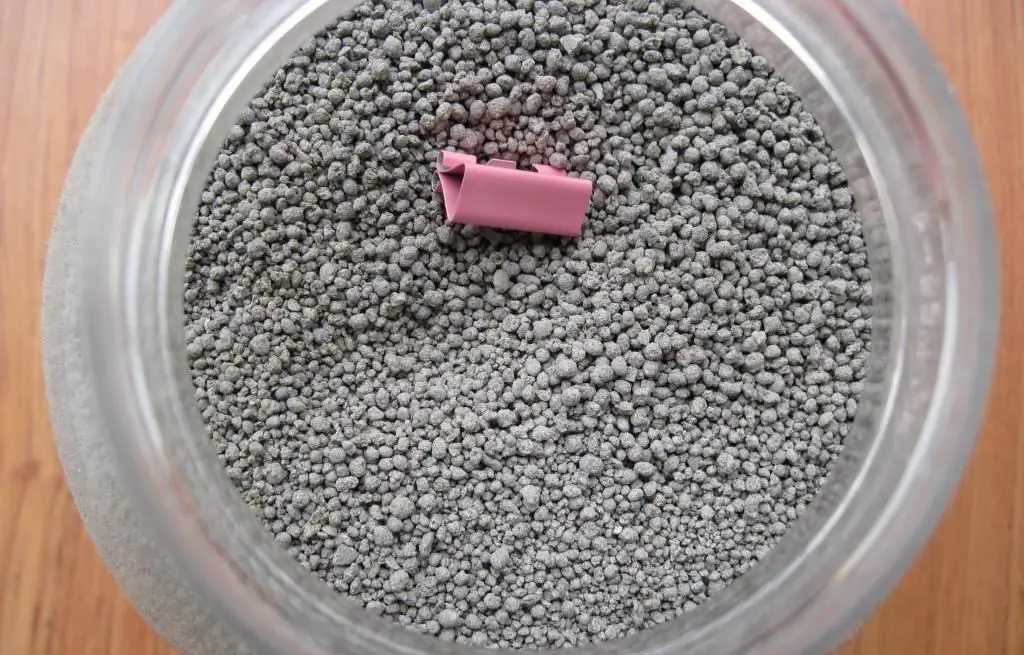
O próprio fluxo, via de regra, é produzido na forma de um pó granulado com uma fração da ordem de 0,2 a 4 mm. Mas o conteúdo e a origem deste produto podem ser muito diferentes e nem sempre uniformes. A este respeito, distinguem-se os seguintes tipos de fluxo para soldagem:
- Óxido. A maior parte do conteúdo é de óxidos metálicos e cerca de 10%é responsável pela proporção de elementos de flúor. Este fluxo é usado para trabalhar com ligas de aço de baixa liga e flúor. Além disso, dependendo do conteúdo, as composições de fluxo de óxido são divididas em sem silício, com baixo teor de silício e com alto teor de silício.
- Óxido de sal. Tais pós também são chamados de mistos, pois o recheio pode ser formado igualmente por óxidos e compostos de sais. Este fluxo é usado para processar ligas de aço.
- Salina. A presença de óxidos é completamente excluída e fluoretos e cloretos formam a base da composição. O objetivo do fluxo de sal é a refusão por eletroescória e soldagem de metais ativos.
Tecnologia de fluxo
Durante o processo de fabricação, a base fundente (lote) passa por diversos processos de processamento, incluindo fundição, granulação, moldagem e controle de qualidade. A matéria-prima da carga antes do processo produtivo é segmentada em pequeno, médio e grande porte. Cada lote passa por uma lavagem e secagem completas, pois a pureza e a precisão nos parâmetros do fluxo futuro são mantidas desde o início. Em seguida, é realizada a pesagem, dosagem e mistura com outros componentes tecnológicos. A fundição e a granulação do fluxo para soldagem são realizadas em equipamentos especiais - são utilizados fornos de chama a gás ou a arco elétrico, piscinas para derramar água fria e paletes de metal. Nas etapas finais do processamento, é realizada a secagem com peneiramento. O fluxo que passou na inspeção é embalado em sacos ou caixas especiais com propriedades refratárias.
Requisitos GOST para fluxo
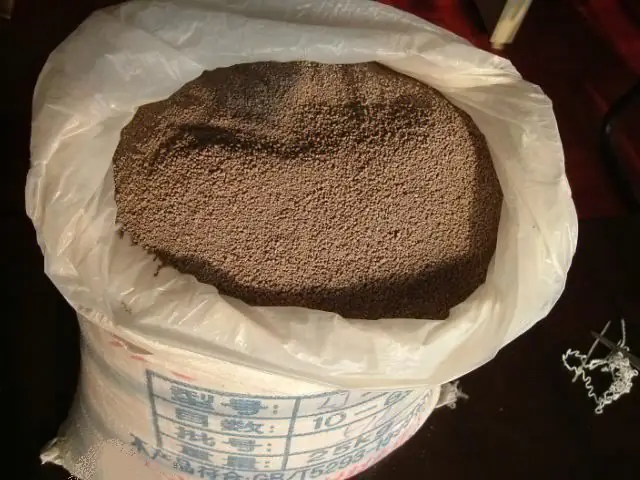
Requisitos regulatórios afetam diversas áreas de avaliação da qualidade do fluxo, bem como regulamentam as regras de segurança para manuseio do material e métodos para testá-lo. Quanto aos parâmetros principais, os seguintes requisitos são impostos a eles:
- Excluído em grãos de pó de fluxo maiores que 1,6mm. A porcentagem de seu conteúdo não deve ser superior a 3% da massa total.
- É permitido produzir um fluxo com fração de até 0,25 mm, desde que esta condição tenha sido inicialmente acordada com o consumidor.
- Além disso, mediante acordo com o consumidor, é permitida a fabricação de material com fração de grão de 0,35 a 2,8 mm, mas somente em relação ao grau AN-348-A.
- O teor de umidade dos fluxos, dependendo da marca, não deve exceder um coeficiente de 0,05 a 0,1%.
Quanto aos requisitos de segurança, as medidas de proteção individual são o principal assunto do regulamento GOST. A soldagem a arco submerso deve ser realizada de acordo com as medidas de segurança contra incêndio. Separadamente, deve-se controlar a concentração do pó de fluxo utilizado, que por padrão é considerado quimicamente perigoso e prejudicial à produção.
Fluxo fundido e não fundido
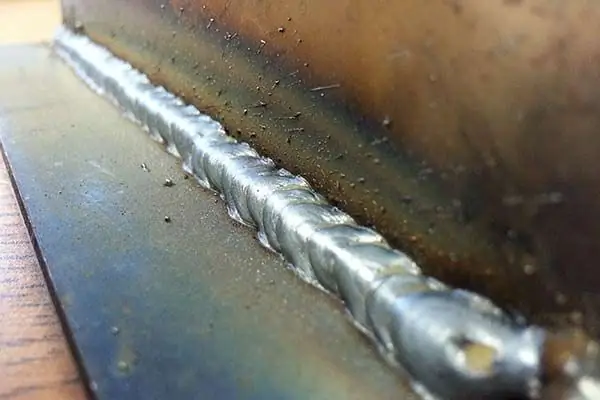
O conteúdo do pó fundido é formado principalmente por componentes formadores de escória. Eles são produzidos como resultado da fusão de elementos constituintes, incluindo areia de quartzo, minério de manganês e giz. Ao misturá-los em determinadas proporções, seguido de fusão em fornos, é possívelobtenha um modificador para uma costura com um determinado conjunto de características. Mais funcional é a soldagem a arco submerso produzida de forma não fundida. Esta é uma mistura de materiais granulados e em pó, que, além da base formadora de escória, também incluem elementos de liga e desoxidantes. A ausência de uma operação de fusão possibilita a introdução de pó metálico e ferroligas no fluxo, o que decifra as possibilidades de melhoria das juntas.
Tipos de soldagem a arco submerso
Com o uso de fluxo, tanto a soldagem manual quanto a automática podem ser realizadas - a diferença fundamental dependerá do equipamento selecionado. A soldagem a arco é realizada no modo autoajustável ou suportada pelo controle automático de tensão. É ideal usar instalações de inversores, complementadas por tambores de alimentação de arame. Também é comum a soldagem com fluxo sem gás, que por padrão atua como um ambiente protetor contra oxigênio e nitrogênio. Qual é a boa técnica que exclui essa barreira aos fatores de impacto negativos? Em primeiro lugar, se um fluxo adequado for selecionado, ele poderá executar toda a lista de tarefas protetoras e auxiliares em relação à costura formada. Em segundo lugar, a ausência de um meio gasoso facilita a própria organização do processo. Não há necessidade de preparar um cilindro com uma mistura de argônio-dióxido de carbono e também proteger a área de soldagem da exposição térmica excessiva ao usar uma tocha.
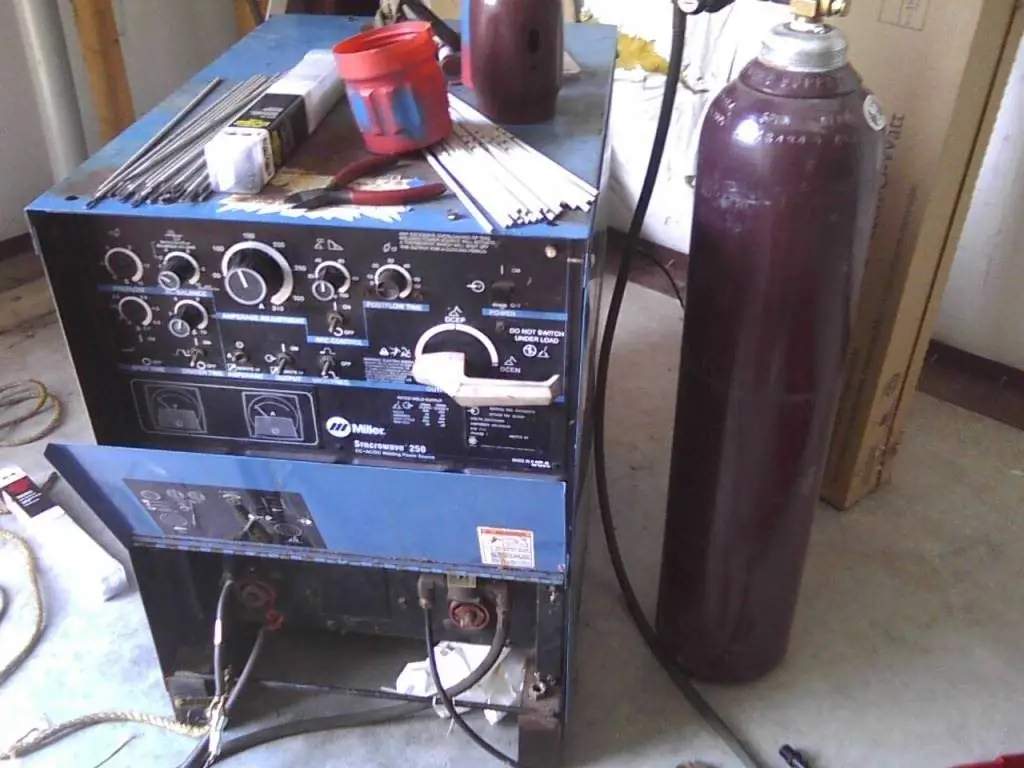
Técnica de fluxo
Após a ignição do arco, o operador deve mantê-loentre a extremidade do eletrodo e a peça sob a camada de fluxo. O pó é derramado em uma camada de 55-60 mm, após o que o arco deve ser literalmente afogado nessa massa até derreter. Com um peso médio de fluxo, sua pressão estática no metal pode ser de cerca de 8-9 g / cm2. Este valor é suficiente para eliminar efeitos mecânicos indesejados na poça de fusão. Ao usar um fio para soldagem com fluxo, é possível obter um mínimo de respingos de fusão. Essa condição é atendida garantindo o contato estável da zona de fusão com o fio consumível e o fluxo, bem como regulando a força da corrente. A proteção do lado do gás também não é necessária neste caso, mas o controle de potência será especialmente importante. Como regra, uma combinação de fio e fluxo é usada ao soldar em alta densidade de corrente, portanto, a máquina deve ser selecionada levando em consideração a manutenção de uma velocidade constante de guiamento da rosca do eletrodo.
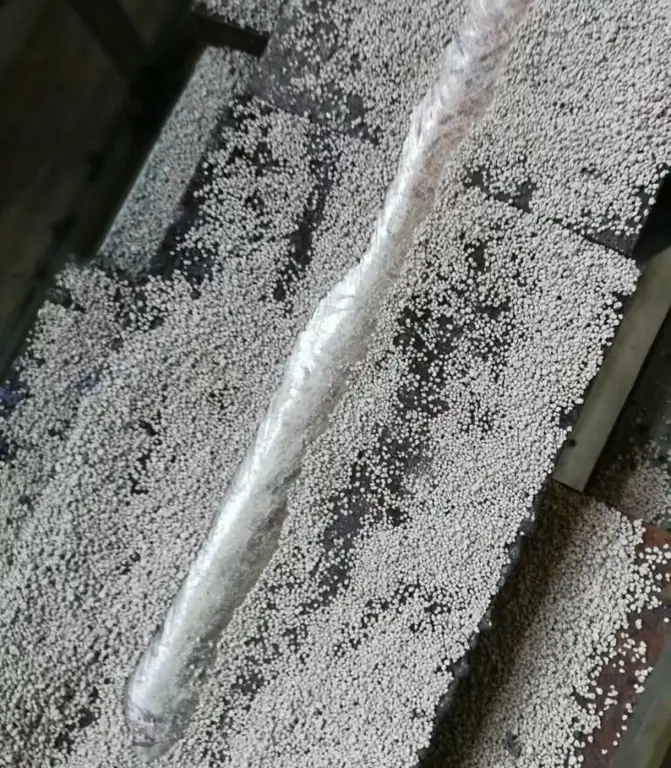
Prós do uso de fluxo
O uso de fluxo certamente afeta a formação da costura da melhor maneira, pois os fatores negativos do processo de trabalho em condições de ar livre são minimizados. Os benefícios óbvios incluem defeitos reduzidos na área da junta, minimização de respingos e controle de arco mais eficiente com recursos completos de controle automático. O que também é muito importante, a área de soldagem a arco submerso é sempre visível para o operador. Isso permite, se necessário, fazer ajustes oportunos no processo e, em alguns casos, até dispensarmáscaras.
Desvantagens do uso do fluxo
Os pontos fracos desta tecnologia são causados por requisitos mais elevados de equipamento, uma vez que é necessária mais potência para derreter o fluxo de forma eficaz. Hoje, são produzidas modificações especiais de dispositivos para soldagem a arco de argônio em ambiente de fluxo, que possuem equipamentos especiais para sua preparação e fornecimento. É lógico que esses modelos custem 15-20% a mais. Outra desvantagem está associada a um aumento na zona de fusão. Embora possa ser controlado dentro de certos limites, é problemático processar pequenos elementos em tais condições.
Conclusão
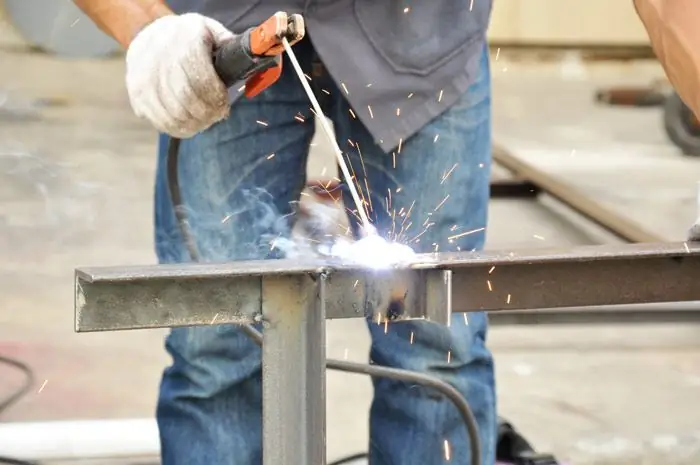
Flux como consumível que melhora a qualidade do processo de soldagem, facilita muitas atividades de produção e construção deste espectro. Mas mesmo em casa, é frequentemente usado no campo, na garagem ou simplesmente em operações de reparo. Ao escolher este material para suas próprias necessidades, é muito importante não calcular mal a avaliação da qualidade. Conforme observado pelo mesmo GOST, o fluxo para soldagem deve ser fornecido ao mercado em sacos de papel grosso de 20 a 50 kg, indicando marcações de transporte. Por encomenda especial, também podem ser feitas pequenas embalagens, mas devem ser fornecidos recipientes especiais para isso. Além disso, a pesagem deve ser realizada com erro máximo de 1% em relação ao peso total da tara.
Recomendado:
Marcador industrial: descrição, composição, regras, aplicação e finalidade
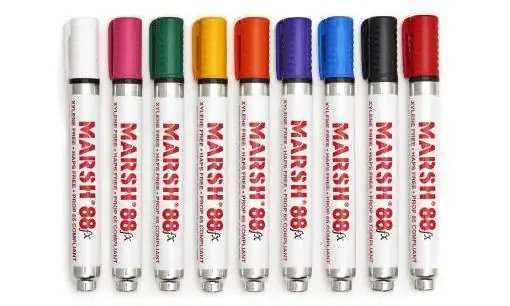
Marcador industrial - uma ferramenta de escrita para aplicar informações em uma variedade de superfícies. Nesse caso, a superfície pode ser madeira, vidro, pedra, metal, couro, materiais pintados e até ferrugem. Os requisitos para tal marcador são muito específicos
Pasta de cimento: propriedades, regras de preparação, composição, conformidade com os requisitos GOST, finalidade e aplicação
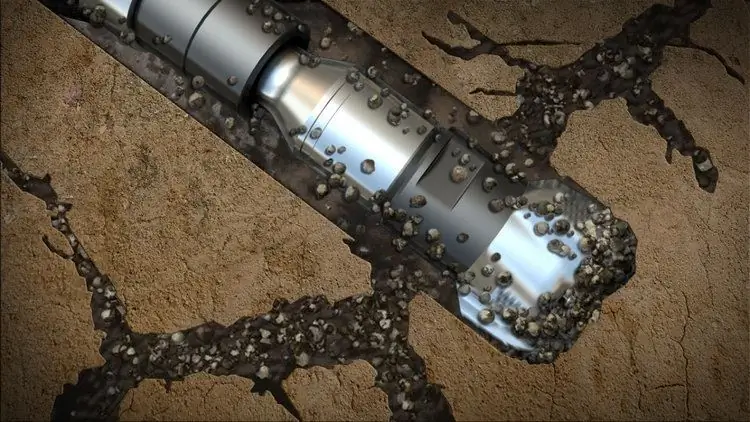
Durante o processo de perfuração, soluções especiais são usadas para remover cascalhos e produtos do desenvolvimento da rocha local. Esta operação é necessária para aumentar a eficiência do impacto mecânico da sonda de perfuração e limpar o fundo do poço. A lavagem é realizada com pastas de cimento, que são preparadas com tecnologias especiais
Argamassa de cimento polimérico: composição, características técnicas, cumprimento dos requisitos GOST, finalidade e aplicação
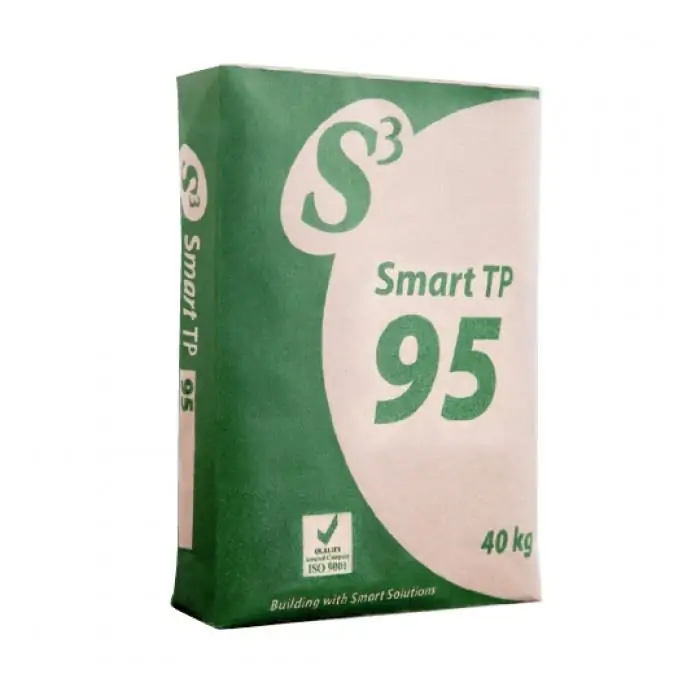
A argamassa de cimento polimérico é uma das modificações da argamassa convencional de areia-cimento. Os polímeros também podem ser adicionados a misturas usadas na colocação de gesso e outros materiais de revestimento. A adição desta substância à composição ajuda a melhorar suas características
Soldadura para soldar cobre, alumínio, latão, aço, aço inoxidável. Composição de solda para soldagem. Tipos de soldas para solda
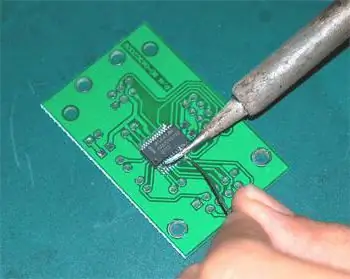
Quando é necessário prender com segurança várias juntas sólidas, a soldagem é mais frequentemente escolhida para isso. Este processo é difundido em muitas indústrias. Temos que soldar e artesãos domésticos
Regulamentos sobre o fluxo documental da organização. Um exemplo de fluxo de trabalho em uma organização
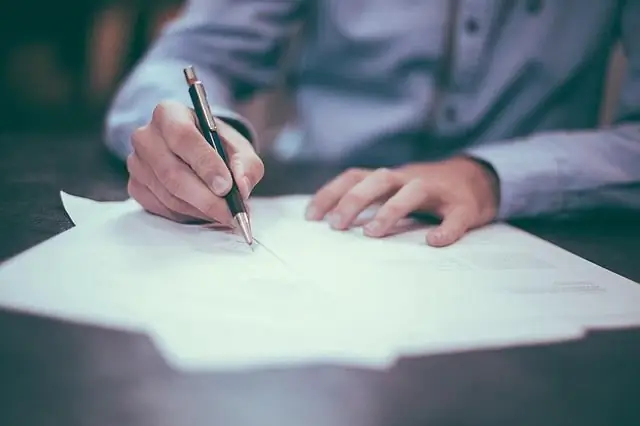
Os documentos são o pulso de uma organização, e o fluxo de trabalho é a vida de uma organização. Os processos e a lógica do movimento da informação em formato escrito e eletrônico determinam o nível de desenvolvimento da organização, sua produção, conquistas socioeconômicas e posição na sociedade. Em última análise, este é um aumento nos lucros e bem-estar dos funcionários